Grinding spherical balls is a crucial process in the manufacturing and maintenance of a range of industrial products. It involves creating perfectly spherical forms from raw materials, which are essential for ensuring efficient performance in various applications, including bearings, valves, and precision instruments. This process demands a high level of expertise, precision, and an uncompromising approach to quality control to ensure the end product meets the rigorous standards required by various industries.
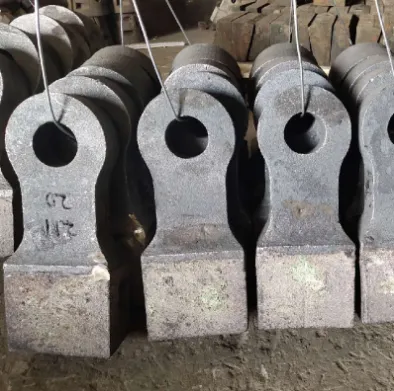
The art and science of grinding spherical balls require a combination of advanced machinery, skilled operators, and the right materials. At the heart of this process is the grinding machine, which must be capable of achieving the high tolerance levels necessary for truly spherical products. The choice of machine depends on the scale, material, and the precision required by the end application. For instance, CNC (Computer Numerical Control) machines are often used for large-scale production lines due to their accuracy and efficiency.
Material selection is another critical aspect of creating spherical balls. While steel is commonly used due to its strength and durability, other materials like ceramic or tungsten carbide are chosen for their resilience and wear resistance in high-temperature or corrosive environments. The selection process involves balancing factors such as the operational environment, desired longevity, and cost efficiency.
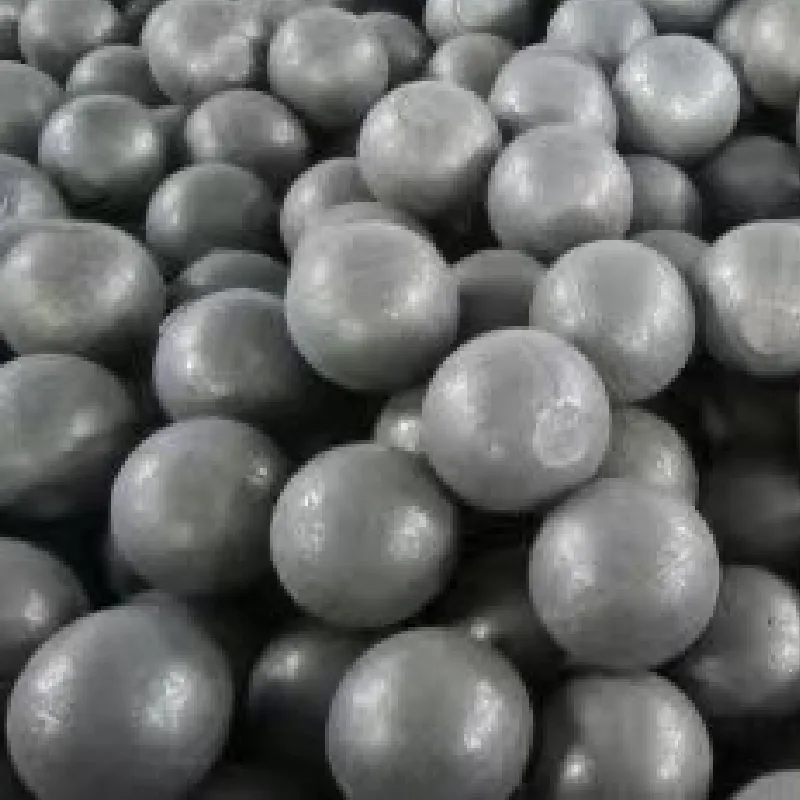
The grinding process itself consists of several stages, including rough grinding, finish grinding, and lapping. Each step is integral to achieving the desired size, roundness, and surface finish. Rough grinding removes the excess material, bringing the ball closer to the desired size. Finish grinding provides a more refined shape, while lapping ensures a smooth surface and perfect sphericity. The use of diamond abrasives in lapping is common due to their hardness and effectiveness in achieving high surface qualities.
Quality control in the production of spherical balls cannot be overstated. In industries such as aerospace, medical devices, and automotive, the cost of failure due to substandard components is high. Therefore, each ball undergoes rigorous testing and inspection to ensure it meets the exact specifications. This includes measuring diameter, checking the surface finish, and inspecting for any defects or irregularities in the material.
grinding of spherical balls
Innovations in this field are continuously evolving with the introduction of advanced technologies such as 3D laser scanning and automated inspection systems. These technologies enhance the precision of the grinding process and ensure that any defects are detected early, reducing waste and improving overall efficiency.
Moreover, the experience and expertise of the production team play a significant role in maintaining the high standards required. Skilled operators are able to adjust machine settings and optimize the process to address any inconsistencies in the material or deviations in machinery performance. Their ability to interpret data from modern inspection technologies is pivotal in maintaining quality and ensuring customer satisfaction.
In addition to technological advancements, adherence to international standards and certifications such as ISO 9001 reinforces the authority and trustworthiness of a company in this field. Compliance with these standards demonstrates a commitment to consistent quality, customer satisfaction, and continuous improvement.
The grinding of spherical balls, therefore, is not just a process but an intricate balance of technology, material science, skilled craftsmanship, and rigorous quality assurance. Its significance across various industries underscores the need for continual investment in research, skilled talent, and advanced technologies to meet the evolving demands of global markets. As the industry progresses, those at the forefront of spherical ball manufacturing stand to gain a competitive edge through enhanced precision, efficiency, and reliability in their products.