Industrial ball mills are essential in the processing of raw materials within various industries, including mining, cement,
and pharmaceuticals. These sophisticated machines are designed to efficiently grind materials into fine powders, thereby significantly enhancing the efficiency and quality of production processes. From personal expertise gathered over decades of engagement in industrial machinery optimization, the notable characteristics and utility of these robust machines cannot be overstated.
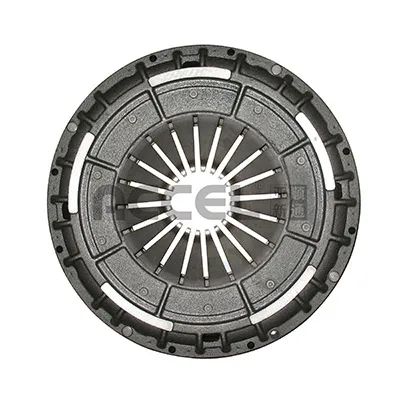
The construction of industrial ball mills is one illustration of their advanced design, comprising sturdy interior components that withstand extreme conditions, favoring long-term durability and minimal maintenance. Their cylindrical steel or ceramic shell is rotated typically by an external source of motor, leading to the friction and impact that facilitate effective grinding. Depending on the application, different media such as steel balls, ceramic balls, or pebbles may be selected to achieve varying results in particle size reduction, reflecting this machine's versatility and adaptability.
Industry experts praise ball mills for their ability to handle both dry and wet grinding processes, a critical factor that contributes to their widespread adoption across diverse sectors. Wet grinding processes are particularly celebrated for their effectiveness in reducing materials to finer consistencies due to the presence of water, which acts as a grinding aid. This adaptability extends to the adjustment of the time and rotation speed, parameters that professionals can tweak for the desired output, offering a customizability not found in many other grinding solutions.
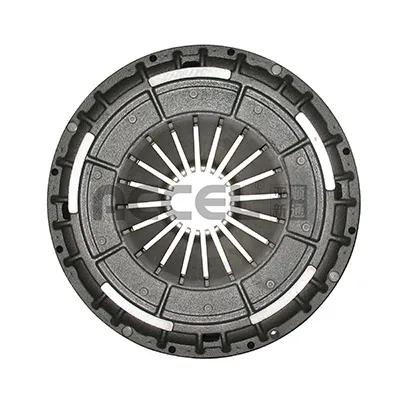
The reliability of industrial ball mills further reinforces their place as a critical component in industrial operations. When discussing equipment trusted for ongoing heavy-duty operations, the robust build and effectiveness of ball mills frequently emerge as a testament to their authority and reliability. Such trustworthiness is evident in sectors where precise material composition and consistency are pivotal, ensuring that the end products meet rigorous standards and industry regulations.
industrial ball mills
Moreover, integrating advanced digital monitoring systems into modern ball mills is instrumental in advancing operational transparency and control—a factor that enhances an organization’s control over process quality and efficiency. Real-time data such as wear and tear, load metrics, and power consumption are monitored, creating opportunities for predictive maintenance and reducing unforeseen downtime. This development emphasizes the expert consensus on adopting smart technologies within traditional machinery to optimize resources and escalate production efficacy.
Environmental concerns are addressed through innovative designs aimed at conserving energy and reducing emissions—a response to both regulatory demands and corporate sustainability goals. This environmentally conscious approach enhances the authoritative standing of industrial ball mills in today’s eco-conscious markets.
Ultimately, the unparalleled combination of durability, precise adaptability, and efficiency exhibited by industrial ball mills validates their critical role across various industries. These machines represent not just fundamental equipment in material processing but are continuously subject to innovation designed to meet evolving industrial demands. Through decades of collective expertise and industry reliance, industrial ball mills have earned their stature as a cornerstone in production lines worldwide.