Mining balls, an essential component of the mining industry, play a significant role in the grinding process of raw materials. These spherical objects are primarily used in ball mills, a type of grinder used to grind or blend materials for use in various processes. Understanding the intricacies of mining balls can enhance operational efficiency, reduce costs, and ensure a sustainable and reliable supply of raw materials.
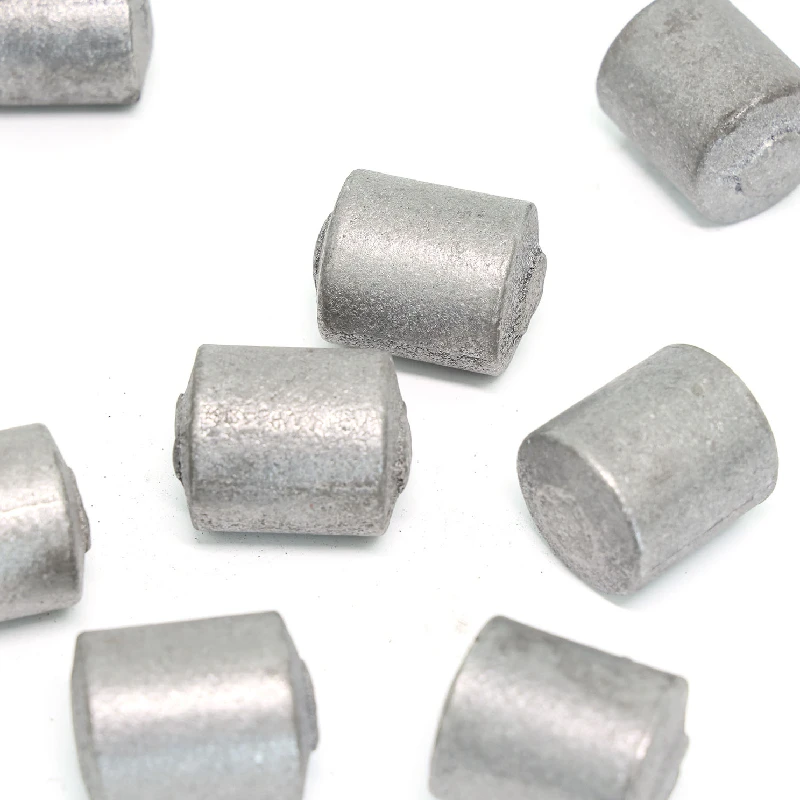
Drawing from the expertise of seasoned professionals in the mining sector, the selection of mining balls involves several critical factors. The material composition is paramount, as it influences durability and performance. High carbon steel is commonly preferred due to its hardness and wear resistance, though alloyed steels are also employed for specific applications.
The hardness of a mining ball significantly affects its lifespan and the grinding process efficiency. Generally, a higher hardness level enhances abrasion resistance, thereby prolonging the ball's operational life.
A firsthand experience shared by a veteran mining engineer underscores the importance of selecting the right diameter for the mining balls. Larger diameters are typically reserved for initial grinding stages, where larger pieces of raw materials need substantial force to break down. Conversely, smaller balls facilitate finer grinding at the latter stages of material processing. Balancing these factors is critical to optimizing the grinding efficiency and ensuring maximum yield.
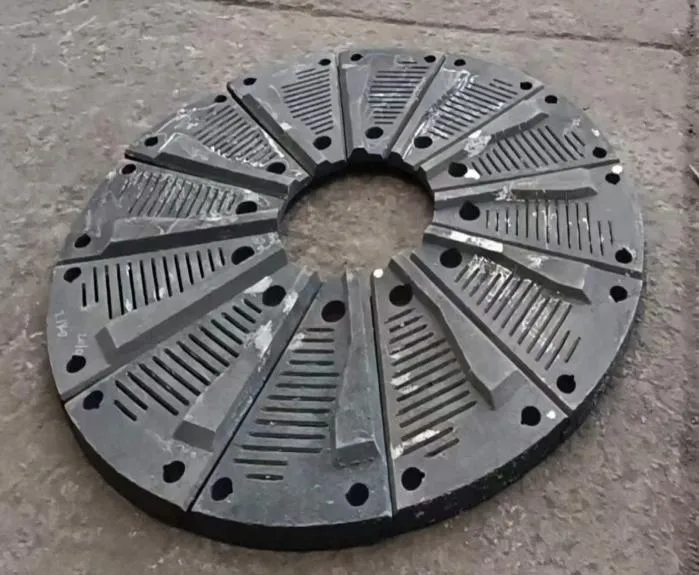
Moreover, an authoritative voice in the industry emphasizes the importance of monitoring the wear and tear of mining balls. Regular inspections and timely replacements are vital to maintaining operational consistency. Excessive wear can lead to reduced milling efficiency, increased energy consumption, and potential breakdowns. Consequently, implementing a robust monitoring system for the wear rate can preemptively address these challenges.
mining balls
It's imperative for mining operations to establish trustworthy partnerships with reputable ball manufacturers. Quality assurance is crucial, as substandard mining balls can cause severe issues in the milling process. Manufacturers should adhere to strict quality control standards, ensuring that each batch of balls meets the specified requirements. Trustworthy manufacturers will also provide documentation verifying the materials and production processes, further enhancing the reliability of the mining balls.
In addition to quality assurance, a reliable supply chain is essential to the seamless operation of mining activities. Disruptions in the availability of mining balls can stall production, accruing substantial financial losses. Collaborating with suppliers known for their consistency and reliability ensures that operations are not hindered by unforeseen supply interruptions.
Integrating advanced technology in the production and selection of mining balls can further augment their effectiveness. The use of computer simulations and modeling allows for virtual testing of different materials and ball sizes, optimizing the milling process before any physical trials. This scientific approach minimizes trial-and-error, saving both time and resources.
Navigating the nuances of mining balls demands a blend of experience, expertise, and vigilance. By choosing the right materials, monitoring wear, and maintaining a robust supply chain, mining operations can achieve enhanced productivity and efficiency. As the mining industry continues to evolve, staying informed about the latest advancements in mining ball technology and adhering to stringent quality standards will ensure that these integral components consistently meet the demands of modern mining operations.