Grinding balls are vital components in the mining industry, playing a pivotal role in mineral extraction processes. These spherical objects, often made of steel, are employed in ball mills to crush and grind various ores. The choice of grinding balls significantly influences the efficiency and output of mining operations. Thus, understanding their characteristics, production, and application is crucial for optimizing mining processes.
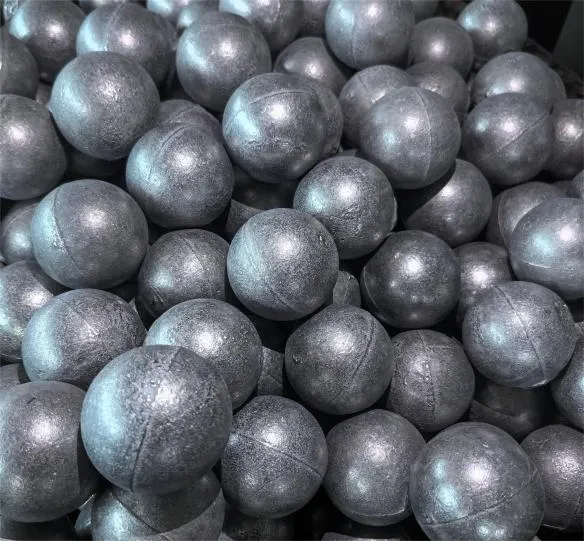
Firstly, the production of grinding balls entails a meticulous process of forging or casting, depending on the desired characteristics and budget constraints. Forged steel grinding balls, for instance, are known for their durability and impact resistance, making them ideal for heavy-duty mining processes. Casting, on the other hand, offers more customization in terms of alloy composition, allowing for specific tailoring to various ore types and milling processes. The choice between forged and cast balls rests largely on the specific requirements of the mineral processing operation.
The material composition of grinding balls is critical. High carbon steel and alloy steel are commonly used due to their wear resistance and hardness. The addition of alloys such as chromium further enhances these properties, providing the strength necessary to withstand the intense pressures of ore grinding. However, achieving the right balance of hardness and toughness is key; overly hard balls can lead to rapid wear of mill liners, while insufficient hardness leads to deformation and rapid attrition of the ball itself.
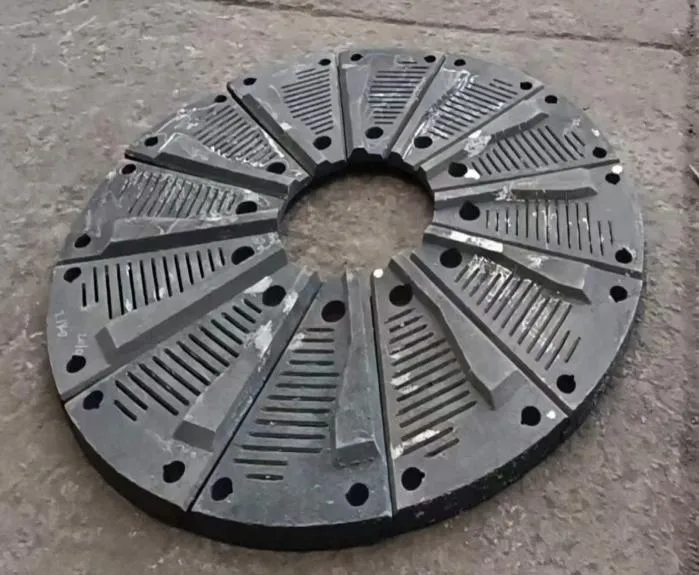
In the mining context, the size of grinding balls is selected based on the size of the ore particles being processed. Typically, larger grinding balls are used for coarser materials, while smaller balls are used for finer milling tasks. The optimal size and ratio of balls must be calculated to ensure efficient use of energy and to achieve the desired granularity.
grinding balls mining
Beyond material and size, the usage pattern of grinding balls impacts overall milling efficacy. This encompasses the lifespan of the balls, their consumption rate, and the operational techniques employed. Regular monitoring of wear rates and performance metrics can inform timely replacement and supply chain adjustments.
Grinding balls not only facilitate the extraction and processing of valuable minerals but also influence the environmental footprint of mining activities. Utilizing high-quality, durable grinding balls reduces waste and energy consumption by improving mill efficiency and lowering maintenance needs. This eco-friendly aspect of using advanced grinding solutions aligns with global sustainability trends in mining operations.
Moreover, incorporating technological advances such as AI and machine learning for predictive maintenance and wear pattern analysis can enhance the lifespan and efficiency of grinding balls. By anticipating wear and scheduling preemptive maintenance, mining companies can minimize downtime and optimize productivity.
In conclusion, the use of grinding balls in mining is a complex process that requires a balance of several factors to optimize performance and efficiency. From selecting the right material and manufacturing process to choosing the appropriate size and monitoring usage patterns, each decision can have substantial effects on overall operation outcomes. As technology continues to advance, integrating smart systems for predictive analysis will likely become a standard in maximizing the potential of grinding balls in the mining industry, ultimately enhancing both profitability and sustainability.