The ball mill liner plate, a crucial component of the grinding machinery, plays a significant role in determining the efficiency and longevity of milling operations. Over the years, my extensive experience in mechanical engineering and materials science has afforded me unique insights into the benefits and selection criteria for high-quality liner plates.
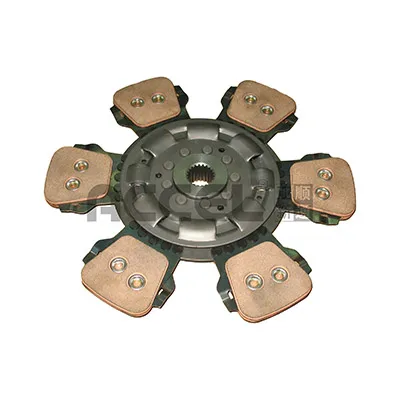
A ball mill, essentially a rotating cylindrical mill, uses grinding media like steel balls to pulverize materials. Central to this process is the liner plate, designed to protect the mill shell and enhance grinding efficiency. The right liner plate can drastically improve productivity by minimizing downtime due to maintenance, hence proving indispensable in various industrial applications, including mining and cement manufacturing.
In selecting an optimal ball mill liner plate, understanding the material science behind these plates is crucial. Typically, liner plates are composed of wear-resistant materials like manganese steel, high-chromium iron, or rubber.
Each material presents distinct advantages. For instance, manganese steel is favored for its high impact forces and resistance against wear and tear. In contrast, high-chromium iron is preferred for its superior performance in high-abrasion environments, despite being slightly brittle. Rubber liners, although less popular, are appreciated in applications requiring excellent noise reduction and minimal energy consumption.
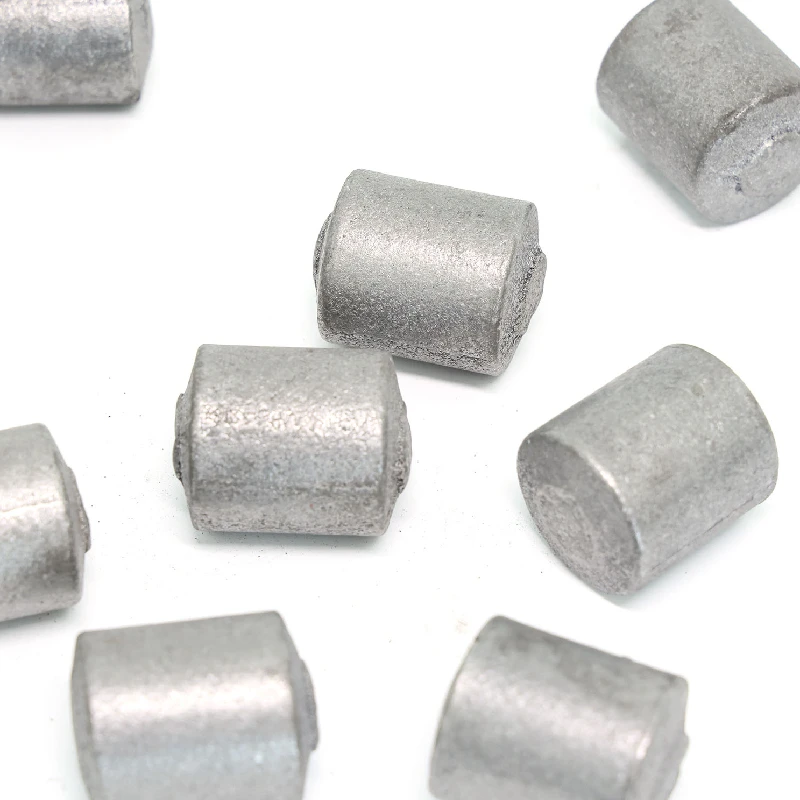
My professional encounters with several mining operations have underscored the importance of choosing the right liner plate material based on the specific milling conditions. Factors such as the type of ore being processed, the rotational speed of the mill, and the mill's operational environment should influence material selection. Ignoring these considerations can result in frequent breakdowns and reduced operational efficiency.
Beyond material selection, the design of the liner plates is equally pivotal. Variations like wave liners, for example, are engineered to improve the lifting action on the grinding media, greatly enhancing the grinding process. Similarly, classifying liners help in segregating the media into different size classes, thereby optimizing the milling process.
ball crusher coating plate
In terms of reliability and authority, working closely with trusted manufacturers who prioritize quality and compliance with industry standards cannot be overstated. Leading manufacturers often employ state-of-the-art technology to produce liner plates that balance durability with performance. Moreover, engaging with vendors offering customization services ensures that the specific needs of a milling operation are met without compromise. Such manufacturers often provide comprehensive installation and maintenance guidance, offering an assurance of product longevity and efficiency.
In practice, an exemplary case involved a mining client who replaced their traditional liner plates with ones tailored to their specific milling conditions. The change resulted in a 20% increase in grinding efficiency and reduced energy costs by a notable margin. This testament to improved performance and cost-effectiveness highlights the value of expert advice and the application of cutting-edge material science.
Establishing trustworthiness in this domain also involves a proactive approach to maintenance. Scheduled inspections and timely replacement of worn-out components avoid costly disruptions. Adopting a predictive maintenance strategy, enabled by modern sensing technologies, offers advanced warning of wear and potential failures, thereby enhancing operational security.
In summary, my extensive background informs me of the criticality of the ball mill liner plate in industrial grinding operations. With the right combination of material and design, businesses can achieve enhanced productivity and reduced operational costs. Those seeking expert advice in the field should consider consulting with industry authorities to navigate the array of options and tailor solutions to specific operational needs. The ongoing advancements in material science and technology promise even more groundbreaking developments in this essential industrial component.