Industry Overview: Evolution of Mill Liner Technology
The mineral processing industry has witnessed significant advancements in mill liners technology over the past two decades. These critical components protect mill shells from wear while optimizing grinding efficiency. According to research published in the Journal of Minerals Engineering, optimized mill liners can increase grinding efficiency by up to 15%, significantly impacting operational costs.
Global Market Insights projects the mineral processing liner market to reach $3.8 billion by 2027, driven by rising demand in mining operations and technological innovations in wear-resistant materials. This growth is particularly pronounced in regions with expanding mining activities like Asia-Pacific and South America.
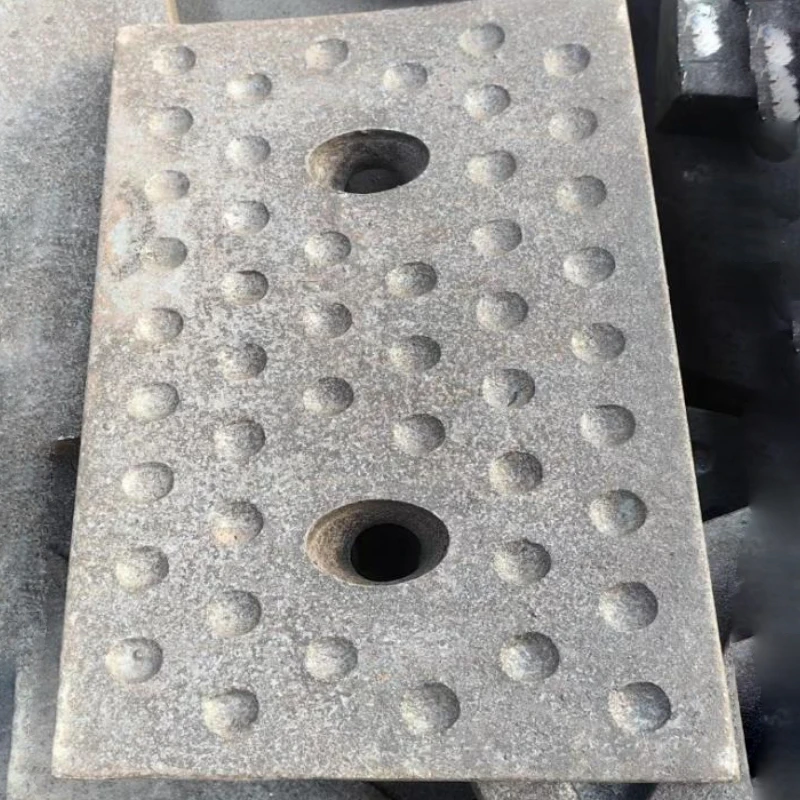
Technical Parameters of Modern Mill Liners
Selecting the proper mill liners requires understanding several critical parameters:
Parameter | Range | Impact on Performance | Measurement |
---|---|---|---|
Hardness | 200-600 HB | Wear resistance | Brinell scale |
Impact Toughness | 20-150 J/cm² | Resistance to cracking | Charpy test |
Liner Thickness | 50-150 mm | Protection lifespan | Millimetres |
Weight | 100-2,000 kg | Installation complexity | Kilograms |
Working Temperature | -40°C to 150°C | Material stability | Celsius |
Shijiazhuang Chengda's Solution: High Manganese Steel Liner
Product Introduction: High manganese steel liner is a kind of wear-resisting material with high strength, wear-resisting and toughness. It is widely used in mining, cement, electric power, iron and steel and other industries.
Technical Superiority: Developed through advanced heat treatment processes, our High Manganese Steel Liners achieve optimal balance between surface hardness (up to 550 HB) and core toughness (impact toughness >100 J/cm²), substantially extending service life in high-impact environments.
View Technical SpecificationsStrategic Selection Guide for Optimal Performance
Selecting between ball mill liners and SAG mill liner configurations requires careful analysis:
Ball Mill Applications
In standard ball mills, rubber composite liners provide superior impact absorption and corrosion resistance. The modular design of modern ball mill rubber lining systems allows for simplified maintenance, reducing downtime by up to 40% compared to traditional steel liners.
SAG Mill Configurations
Semi-autogenous grinding mills require specialized SAG mill liner designs incorporating lifters and shell plates engineered to handle large ore particles. Recent designs focus on optimizing grinding media trajectories, with research showing properly configured liners increase throughput by 8-12%.
Installation & Maintenance Protocols
Proper installation of mill liners follows strict engineering guidelines. The Global Mining Standards and Guidelines Group (GMSG) recommends:
- Shell preparation to ISO 8501-1 Sa2.5 cleanliness standard
- Torque sequencing following manufacturer specifications
- Liner alignment within 2mm tolerance
- Post-installation clearance checks
Innovative locking systems from leading manufacturers like Shijiazhuang Chengda have reduced liner replacement time from 48 hours to under 24 hours in typical installations, significantly impacting mill availability.
Material Technology Innovations
The evolution of mill liners materials has progressed through several generations:
- First-generation: Standard carbon steel (20,000-35,000 operating hours)
- Second-generation: High-chrome alloys (35,000-50,000 hours)
- Third-generation: Rubber-metal composites (40,000-60,000 hours)
- Advanced generation: Nano-structured steel alloys (60,000-85,000+ hours)
Shijiazhuang Chengda's High Manganese Steel Liner represents the cutting edge in material technology, with micro-alloying elements enhancing work-hardening properties to achieve surface hardness exceeding 550 HB under operational conditions.