Understanding the factors that influence the price of steel grinding balls is crucial for businesses in industries such as mining, cement production, and metal manufacturing. One primary factor impacting cost is the raw material itself. Steel production has inherent complexities, and fluctuations in global steel prices can directly affect the cost of grinding balls. Companies utilizing these products should be mindful of global market trends in raw material supply and demand.
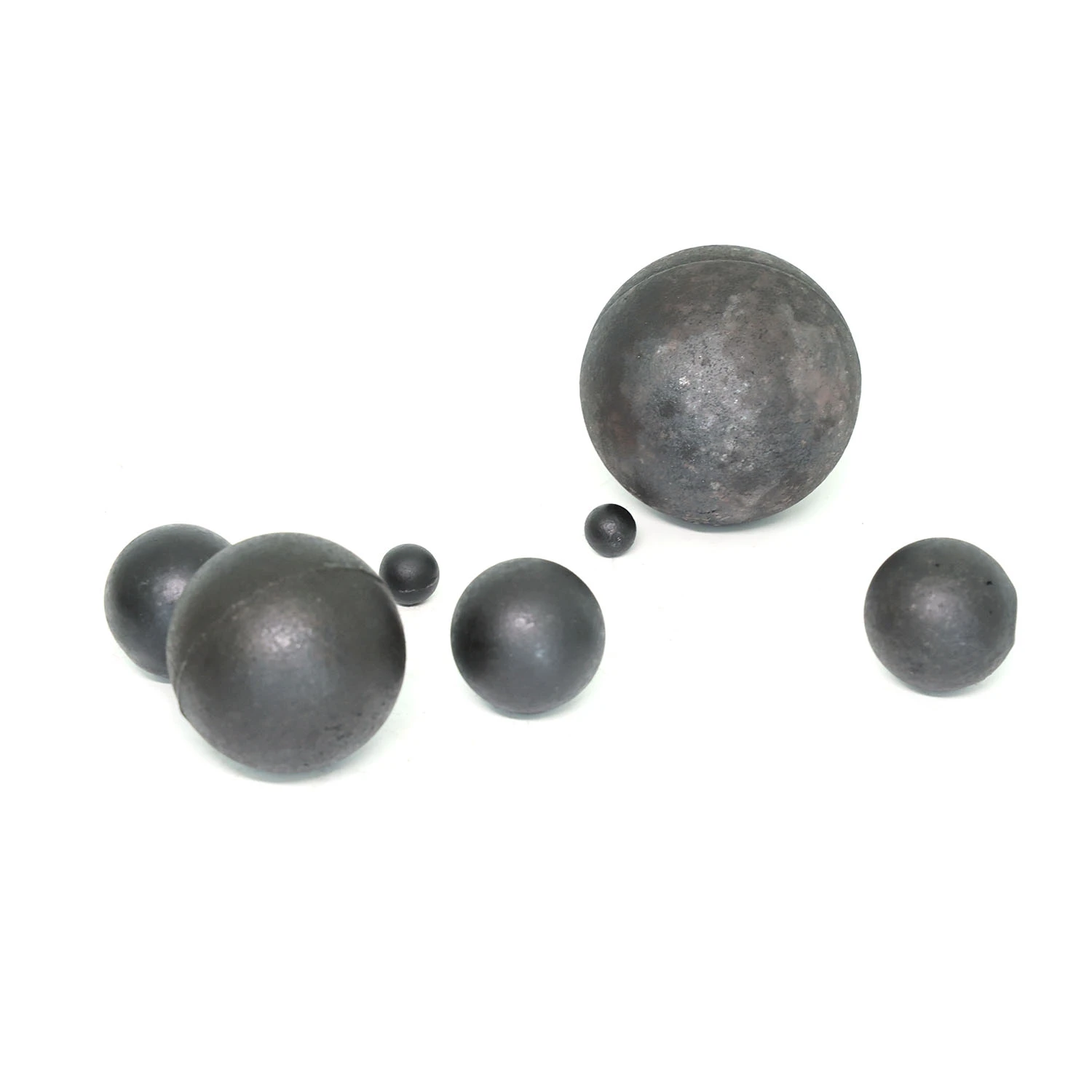
Additionally, the manufacturing process and technology used play significant roles in pricing. Advanced methods and machinery can enhance efficiency and precision, reducing waste and potentially lowering costs. However, the initial investment in technology might increase the overall price of high-quality grinding balls. The selection of manufacturing techniques, whether traditional or state-of-the-art, thus greatly influences the end price.
The quality and durability of the balls are other critical considerations. High-chromium balls, known for their wear resistance and longer service life, might carry a higher price tag but can lead to cost savings over time due to reduced replacement frequency. Organizations should assess their operational needs and determine whether investing in higher-quality, albeit more expensive, grinding balls will yield long-term economic benefits.
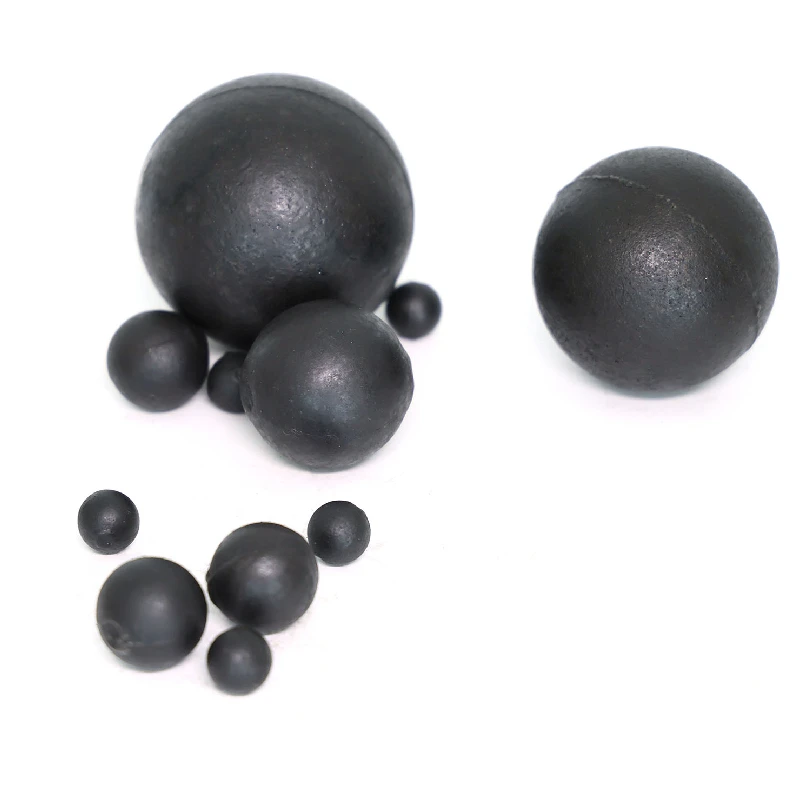
Production volume impacts cost per unit, where bulk purchases can lead to significant discounts. This is particularly relevant for large-scale operations that continually require grinding media. By negotiating contracts with established suppliers, companies can leverage volume discounts and secure more favorable terms, balancing the upfront costs with operational demands.
Moreover, additional services offered by suppliers, such as custom ball sizes, tailored chemical compositions, and specialized heat treatment processes, may also influence pricing. These customizations, while enhancing performance and efficiency, can introduce additional costs. The decision to opt for bespoke solutions should therefore be weighed against operational efficiency gains and overall cost-effectiveness.
price of steel grinding balls
Transportation and logistical considerations are also salient, as they influence the net price paid for these grinding balls. Shipping costs can vary based on distance, weight, and geographic restrictions. Hence, local sourcing might be an appealing option to reduce transportation-related expenses, provided that quality isn’t compromised. Furthermore, working with established suppliers who have a solid logistical framework can mitigate unexpected delays and associated costs.
The reputation and reliability of suppliers impact perceived value and price. Trusted suppliers with a record of consistent quality and service might charge a premium. However, engaging with such vendors assures businesses of receiving dependable products and superior customer service, reducing the risks associated with project delays or operational inefficiencies.
Lastly, sustainability considerations are increasingly influencing purchasing decisions. Companies are progressively prioritizing suppliers that adhere to stringent environmental and ethical standards, sometimes at a higher cost. Embracing sustainable purchasing aligns with global corporate responsibility trends and can bolster brand image, while potentially qualifying businesses for green initiatives and tax incentives.
By comprehensively understanding these factors,
businesses can make informed decisions when purchasing steel grinding balls. Analyzing quality, cost, supplier reliability, and sustainability allows companies to balance performance requirements with financial prudence, ensuring optimal investments in grinding media.