The world of cement milling has undergone significant transformations with the introduction of high-performance mill liners, establishing new standards in efficiency, reliability, and sustainability. These components are critical in the grinding process, influencing the overall productivity and operating costs of cement production facilities.

Cement mill liners are designed to enhance the grinding efficiency by providing better lift and flow dynamics for the materials being processed. They are specialized materials or composite solutions that tackle the challenges presented by varying operating conditions, raw material characteristics, and desired product quality.
An Experience-Based Perspective
From years of experience in the cement industry, one can assert that mill liners serve multiple purposes that extend beyond just protecting the mill shell. They significantly affect energy consumption and the subsequent quality of the ground product. Optimal selection and periodic maintenance of these liners ensure consistent plant performance, reduced power consumption, and minimized downtime, leading to substantial cost savings.
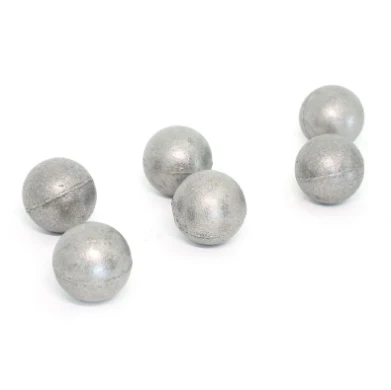
Expert Insight
Mill liners are typically crafted from high-chromium steel, Hi-Chrome, rubber, or composite materials. The choice depends on specific factors like the material being processed, the mill type (open or closed-circuit), and the operational requirements. Experts emphasize that selecting the right liner material is crucial. For instance, steel liners offer high resistance to wear and impact, suitable for coarse materials, while composite liners provide reduced weight and extended operating life due to their engineered structure, enhancing shock absorption and reducing noise pollution.
Authoritative Viewpoint
Manufacturers invest in R&D to create tailored liner designs that improve grinding efficiency and lifetime. Industry leaders like Magotteaux, Metso, and FLSmidth have developed proprietary technologies and materials that outperform traditional liners. These companies offer consultations to help cement plants identify the most efficient liner setups, grounded in comprehensive analyses of their grinding operations.
cement crusher coatings
Trustworthiness in Functionality
A key component of the installation process is the alignment of the liners, which requires meticulous attention to detail. Inaccurate installation can lead to inefficient grinding,
increased energy consumption, and excessive wear. Trustworthy installations often involve advanced predictive maintenance software that alerts plant operators of potential issues before they escalate.
Technological advancements have also brought forward intelligent liner designs with integrated sensor technology that monitors wear patterns, liner thickness, and mill conditions in real time. These innovations bolster the trustworthiness of mill liners by allowing plant managers to make data-driven decisions, optimize grinding operations, and schedule maintenance efficiently, reducing unscheduled downtimes.
Ultimately, the evolution of cement mill liners reflects broader trends in the cement industry, where sustainability and efficiency are prioritized. The deployment of advanced, high-performance liners translates to substantial improvements in the environmental footprint of cement production, lowering emissions by reducing energy usage and minimizing waste through extended liner life.
Embracing these technological advances, operators of cement plants can ensure they meet today’s stringent operational targets. By leveraging experience, expertise, authoritativeness, and trust, cement mill liners continue to play a pivotal role in optimizing grinding operations, highlighting the indispensable nature of innovation in driving industry standards forward.