Selecting the appropriate size for grinding balls is crucial in optimizing the performance of ball mills, enhancing efficiency, and ensuring cost-effectiveness in the grinding process. Professional experience shows that using the right size of grinding media can significantly impact productivity in industries such as mining, cement, and chemical manufacturing. Understanding the components that influence the selection can vastly improve operational outcomes.
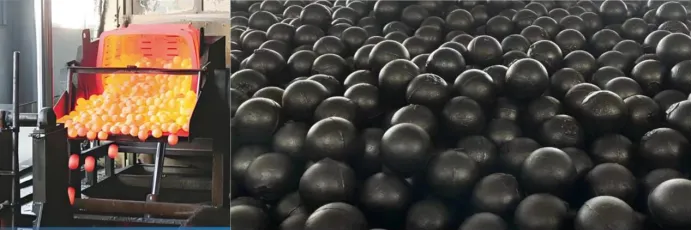
Industry experts consistently emphasize the importance of understanding the material being processed. Materials have varying hardness, size distribution, and abrasiveness,
influencing the choice of grinding ball size. For instance, harder materials require larger and more robust grinding balls to effectively break them down without excessive wear on milling equipment.
In addition to material characteristics, the milling environment plays a crucial role. The ball mill's working conditions, such as speed, temperature, and milling time, must be considered. Adjustments to ball size can optimize these variables, ensuring that the milling process is efficient and effective. For example, a faster milling speed might necessitate smaller balls to prevent excess energy and heat buildup, which can lead to premature wear or material degradation.
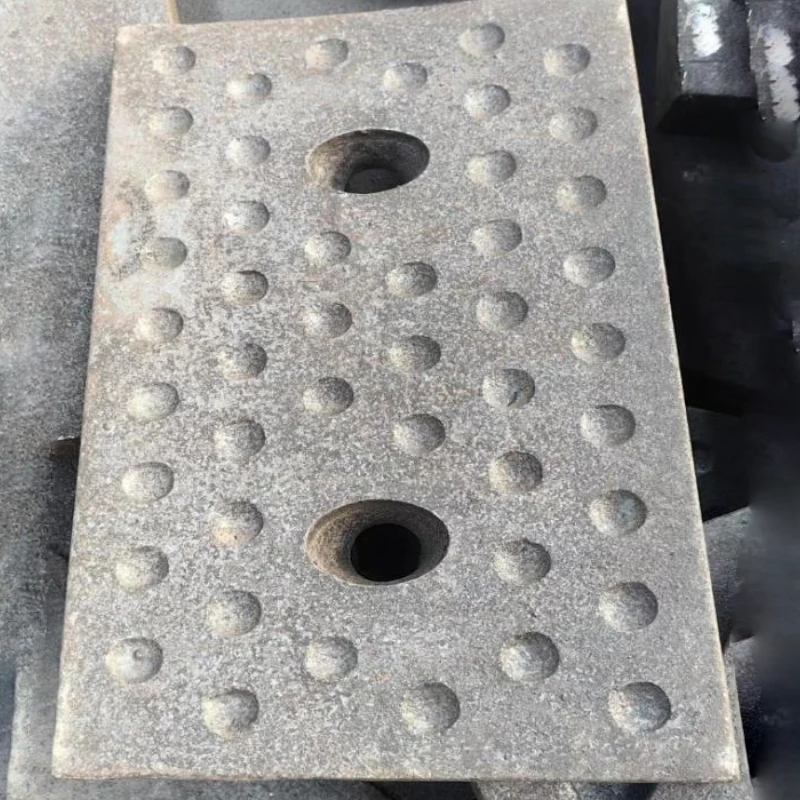
Reliable data from field reports suggest that smaller balls provide a larger surface area and better capability for fine grinding, while larger balls are optimal for coarse grinding tasks. This is due to the differing impacts of the kinetic energy involved smaller balls offer a more even energy distribution suitable for breaking down finer particles, whereas larger balls exert more forceful impacts, essential for breaking down larger material chunks.
Furthermore, the consistency and uniformity of size across the ball media can prevent issues such as uneven grinding or overstressing of the mill, which can lead to mechanical failures. It becomes vital, therefore, to maintain strict quality controls during the production of grinding balls to ensure consistency in size and mix.
selection of grinding ball size
Trusted industry studies reveal that optimizing the loading and size mixture of balls can further enhance grinding efficiency. A research-backed approach known as the Bond formula provides a reliable guideline for determining the ideal ball size. By using a mathematical relationship that considers ore-specific parameters like work index and desired product size, this formula helps in deriving a scientifically sound ball size recommendation.
Implementing such sophisticated selection methods not only improves efficiency but also ensures resource conservation and cost savings. By tailoring the size of the grinding balls to the specific milling requirement, less energy is wasted, and the overall milling operation becomes more cost-effective. This is of particular importance in resource-intensive industries aiming to improve sustainability and operational efficiency.
For robust and reliable operation, it is also important to source grinding balls from reputable manufacturers who can provide documentation of ball composition, hardness, and size distribution. This level of transparency builds trust and assures end-users of the grinding media's quality, fostering a reliable partnership that aligns with long-term operational goals.
In summary, the selection of the right grinding ball size is an intricate process that combines an understanding of material science, milling dynamics, and empirical research. By leveraging expertise and data-driven methodologies, industries can significantly enhance milling performance, leading to improved productivity, reduced operational costs, and a more sustainable use of resources. A strategic approach to ball selection, underscored by trust and authority in supplier relationships, is vital in achieving these outcomes.