Choosing the right size of grinding ball is crucial in the milling process, playing a significant role in optimizing mill performance, achieving efficient breakage, and ensuring cost-effectiveness. As an experienced industry professional involved in the selection and integration of grinding balls for various milling applications, I suggest a comprehensive approach involving experimentation, analysis, and expertise to make the best choice for your specific operational needs.
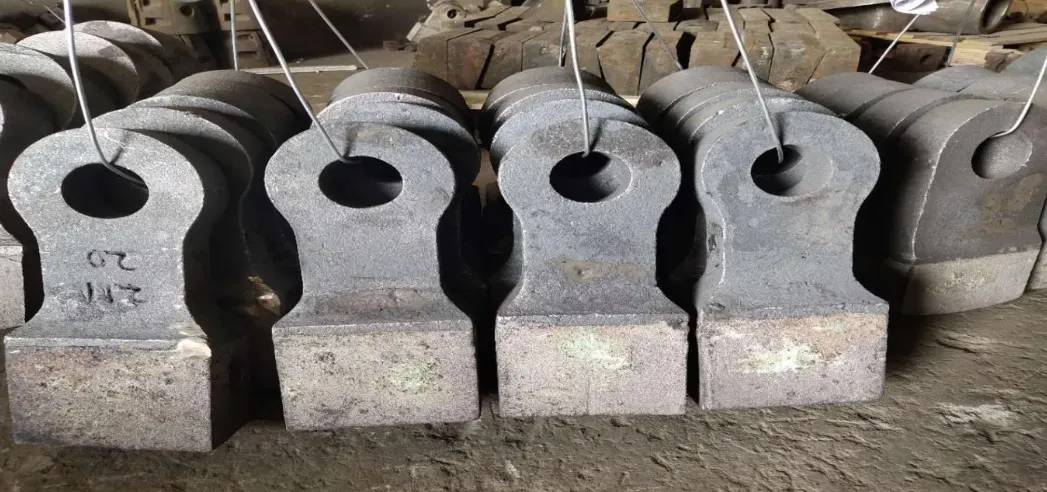
First and foremost, it is essential to understand the material being processed and the desired end-product quality. Different materials and desired outcomes often require varying sizes of grinding media. Harder materials typically necessitate smaller grinding balls to efficiently break down particles, while softer materials might benefit from larger balls to avoid excessive wear and tear. A precise understanding of the material properties guarantees that the selected grinding ball size will enhance the milling efficiency and product quality.
Particle size distribution of the feed material should also be carefully considered. Measuring and analyzing the size distribution provides insight into the required reduction in particle size, aiding in determining the optimal size of the grinding ball. Operations dealing with larger feed sizes can experiment with larger grinding balls that possess the energy to break even the most challenging particles, while those with finer feed can economize with smaller sizes, optimizing the throughput and energy consumption.
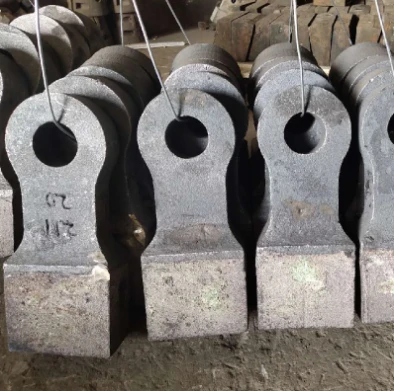
Another critical aspect is the type of mill used in the operation. Each mill type, whether it be a ball mill, a SAG (semi-autogenous grinding) mill, or a rod mill, has distinct working principles and dynamics that impact the ideal selection of grinding ball size. For instance, ball mills often benefit from a combination of ball sizes to ensure thorough grinding and reduced void spaces for optimal contact with material particles.
selection of grinding ball size
Additionally, wear rate and durability of the grinding balls must be factored into the selection process. Economic considerations often dictate that the chosen grinding ball should not only be effective in its function but also durable enough to ensure longevity and reduce frequent replacement costs. Here,
the quality of the material from which the grinding ball is made becomes significant. It's advisable to consult with manufacturers or suppliers with proven reputations for delivering durable and high-quality grinding media.
Acquiring insights from real-world case studies and testimonials from similar milling operations can also be invaluable. Implementation of proper monitoring tools to track mill performance and grinding ball efficacy can provide empirical evidence that verifies initial assumptions and recommendations.
Lastly, achieving the correct balance in grinding ball size also incorporates considering the operational conditions of the mill, including speed, load, and mill efficiency. Adjustments should be made based on data analytics and historical performance analyses, ensuring that size selection is dynamically responsive to changing operational demands.
Access to these advanced methodologies and professional insights transforms the selection process of grinding ball size from mere estimation into an authoritative, expert-guided endeavor. This expertise-driven approach ensures that you're able to trust the reliability of your milling operation, optimizing output while maintaining cost-effectiveness, thus aligning with the best practices in the industry.