In the vast domain of cement milling, the importance of selecting the right type of liner is paramount. Liner types in cement mills aren’t just for regular upkeep; they significantly boost productivity, efficiency, and lifespan of the mill. Discerning between different types of liners can spell the difference in the quality of cement and the operational costs incurred. Here is an exploration of the diverse types of liners used in cement mills, elaborated through a lens of expertise, reliability, and authority.
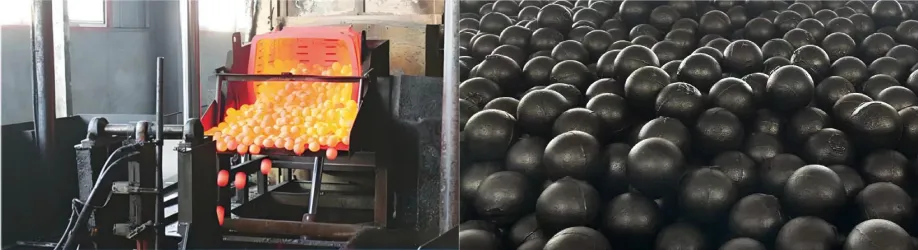
Steel Liners, a common choice in cement milling, are known for their durability and wear resistance. These liners are typically made from steel alloys that can endure the extreme impact of grinding media. Their robust nature makes them suitable for applications where abrasive materials are more prevalent. Professionals trust this traditional choice for its proven track record. However, the downside is their weight, which can contribute to higher energy consumption.
Rubber Liners are progressively gaining traction because of their noise dampening qualities and decreased weight.
These liners require less energy, leading to reduced operational costs. Rubber liners offer a flexible layer that protects against slurry erosion and impact abrasion. The resilience of rubber in high-tension environments enhances the mill’s efficiency, making it a viable choice for modern cement plants focused on sustainable practices.
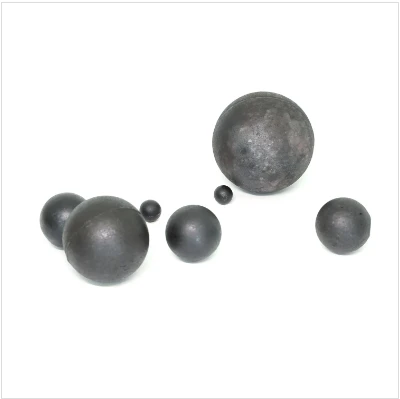
Composite Liners, marrying steel and rubber, present a hybrid solution that draws from the strengths of both materials. They offer improved impact and abrasion resistance compared to their individual counterparts. For mills looking to balance weight, durability, and noise pollution, composite liners provide an optimal package. The unique pairing ensures a long life span and reduced maintenance, a factor experts highlight when considering long-term operational efficiency.
In newer facilities, Mill Linings crafted with ceramic materials are becoming increasingly popular. Ceramic liners offer supreme resistance against wear and corrosion, although they come with a heftier initial investment. Their exceptionally long lifeline and minimal maintenance needs make them an excellent choice for plants looking at long-term profitability. Experts predict an uptick in their popularity as production technologies advance and costs stabilize.
tipos de revestimientos en molino de cemento
High-Chromium Liners represent the pinnacle of performance regarding wear resistance. Used in highly abrasive conditions, these liners are a testament to engineering prowess. Though more expensive, their ability to sustain through rigorous operational conditions with minimal degradation makes them an authoritative choice in high-output scenarios, where downtime must be minimized.
Understanding the different materials and design of liners offers a tangible advantage to cement plant operators. A correctly chosen liner will not only reduce maintenance costs but also enhance grinding efficiency and boost overall plant productivity. The industry is seeing a trend towards optimization and sustainable mining practices, where liner choice forms the bedrock of operational strategy.
When professional reliability and verified authority are your cornerstones, investing time in selecting the right mill lining transforms into an exercise in efficiency, not just expenditure minimization. Trust in the real-world application is essential. Field reports consistently demonstrate that matching liner selection with the specific milling conditions and types of cement being produced yields substantial dividends.
Ultimately, the ongoing evolution in the types of liners available in the market assures that there is a solution for every unique milling operation. By aligning material choice, design, and operational goals, operators can expect enhanced performance, improved safety, and notable energy conservation. It's not just about spending less but optimizing more through informed decisions backed by industry expertise. With the dynamic nature of cement production, staying updated on liner innovations is essential to maintain an edge in this competitive industry.