Cement mills are integral machines in the manufacturing of cement, serving the essential function of grinding the clinker to a fine powder. One critical component that determines the efficiency and longevity of these mills is the type of lining or coating used. Understanding the different types of linings and their applications can not only enhance operational performance but also significantly reduce operational costs.
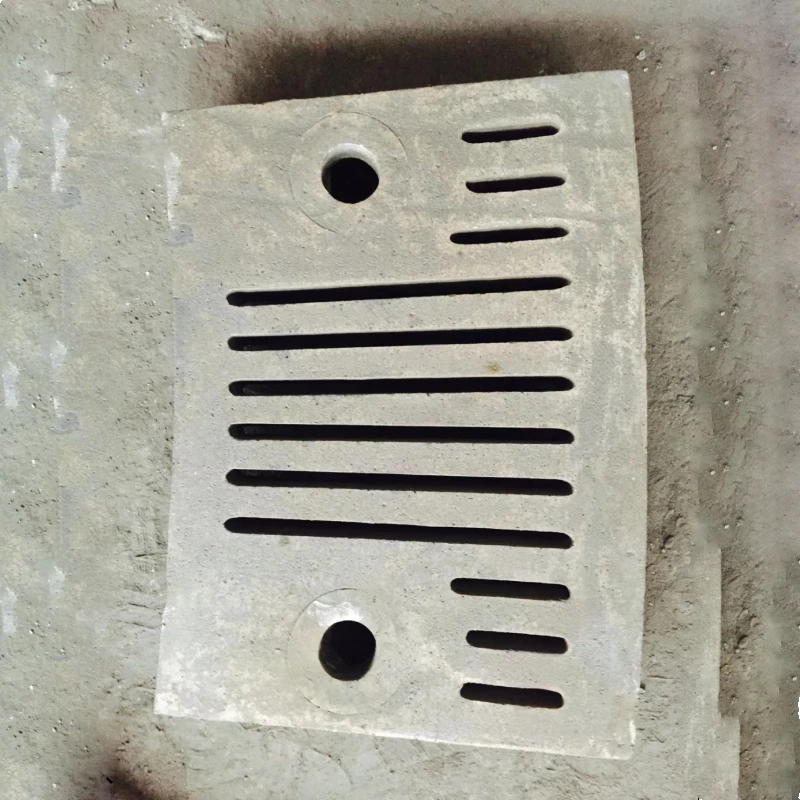
In the complex world of cement mill operation, coatings play a vital role in protecting the mill from wear and tear, enhancing efficiency, and maintaining consistent product quality. The importance of selecting the right type of lining cannot be overstated, as it can affect everything from power consumption to product homogeneity and even environmental compliance.
Types of Linings in Cement Mills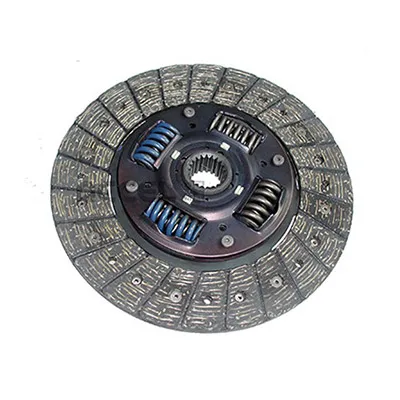
1. Metal Linings Traditionally, metal linings, typically made from alloys of steel, have been the go-to choice for durability and strength. These linings are ideal for mills that process highly abrasive materials. The metal's robustness offers exceptional tolerance against impacts, making it suitable for mills experiencing high-frequency vibrations and severe operational conditions.
2. Rubber Linings An increasing number of cement producers are switching to rubber linings due to their flexibility and ability to dampen vibrations. Rubber linings reduce the noise levels in the mill and offer good resistance against corrosive and abrasive wear, thus extending the lifespan of the mill. They are particularly effective in mills where moisture levels are high, helping prevent rust and corrosion.
3. Composite Linings Combining the strengths of both metal and rubber, composite linings offer enhanced impact resistance and abrasive wear protection. They can efficiently accommodate variations in material load and provide a cost-effective solution with reduced maintenance needs. These linings strike a balance between the durability of metal and the resilience of rubber, making them suitable for a wide range of milling conditions.
4. High Alumina Linings These are recommended for mills that require grinding finer particles. High alumina linings present a smooth surface, reducing the likelihood of material buildup and offering excellent wear resistance. They promote minimal contamination of the material being processed, ensuring product purity and quality.
Types of coatings used in cement crushers
5. Ceramic Linings Known for their exceptional hardness and wear resistance, ceramic linings are suitable for milling operations that involve highly abrasive materials. Although more costly than other types, ceramics provide a significant return on investment through decreased downtime and maintenance, and increased mill throughput.
Choosing the Right Lining
Selecting the appropriate lining for a cement mill involves analyzing the characteristics of the materials being processed, operational parameters, and the desired product outcome. Evaluating factors such as abrasiveness, material size, moisture content, and milling speed can guide you to the most effective lining solution.
For new installations or liner replacements, consulting with manufacturers or technical experts can ensure the chosen lining matches the specific operational demands. Regular maintenance and performance assessments can also extend the lifespan of the linings, reduce unexpected shutdowns, and maintain optimal milling efficiency.
Conclusion
The choice of lining in a cement mill is crucial for optimizing operational performance and ensuring longevity of the mill itself. Each type of lining possesses unique attributes, making it important to align these characteristics with the specific needs of your milling process. Embracing a data-driven approach and leveraging technical expertise can significantly enhance efficiency and reduce costs, thus providing a sustainable competitive edge in the cement industry. This strategic choice not only impacts the bottom line through reduced maintenance costs and improved production rates but also enhances the product quality that ultimately reaches the end consumers.