Selecting the right grinding media for a ball mill is a crucial factor in optimizing the efficiency and performance of the milling process. High-quality grinding media can improve productivity, reduce costs, and ensure that the final product meets desired specifications.
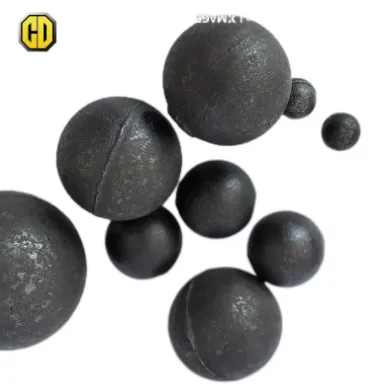
Having worked extensively in the field of materials engineering and industrial processes, I can assert that the choice of grinding media in a ball mill cannot be understated. One must consider several factors when selecting these components material composition, size, shape, and the operating conditions of the mill.
Material composition plays a significant role in the effectiveness of grinding media. The media should be made from materials that are wear-resistant and durable, ensuring longevity in various processing environments. Common materials include steel, ceramic, and flint, each tailored for specific applications. Steel grinding media is generally used when dealing with coarser materials, whereas ceramic grinding media is preferred when a finer product is needed without contamination.
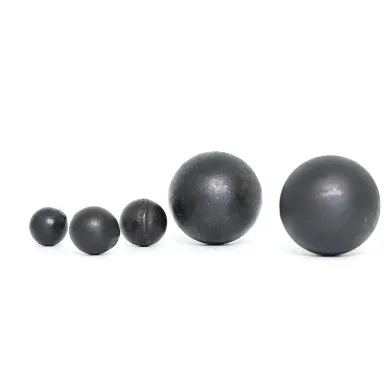
Size and shape are equally critical. The diameter of the media affects the grinding efficiency; larger media are suitable for crushing larger particles, but may compromise the granularity of finely processed materials. Smaller media offer more interactions and should be used when a finer grind is essential. The shape of the media, often spherical, is designed to reduce friction and increase grinding efficiency, but variations like rods or cylinders can be applied for specific milling needs.
From an expertise standpoint, the milling environment substantially dictates the suitable grinding media. Variables such as mill speed, liner designs, and lifter configurations must synchronize with the chosen media to maximize milling efficiency. Experienced professionals often conduct thorough testing under different operating conditions to determine the optimal configuration that meets production demands.
мелющие тела шаровой мельницы
Trust in the manufacturers of grinding media is another vital component. Reliable manufacturers provide detailed technical data and quality assurance, ensuring that their media can withstand the mechanical stresses imposed during milling. They often supply specifications like hardness, density, and chemical composition, facilitating informed decisions for specialists in material procurement.
As a dominant figure in the milling industry, I advise stakeholders to engage in a comprehensive evaluation process before selecting grinding media. Consideration must be given to the cost-benefit analysis over the lifecycle of the media. Long-term savings in terms of increased productivity and reduced equipment wear can justify investments in higher-quality grinding media.
Ultimately, achieving the delicate balance of cost efficiency, operational performance, and product quality hinges on informed choices and expert application of grinding media. Emphasizing this decision-making process is paramount to maintaining competitive advantages in the evolving marketplace, where consistent and precise outputs can significantly impact market positioning.
With this knowledge, specialists in milling operations can enhance their systems' productivity and reliability, leading to distinguished success in their respective industries.