The grinding ball mill remains an essential tool in the mineral processing industry, a linchpin in achieving finely milled materials, critical for downstream processing. Its significance is drawn not only from its time-tested efficiency but also from evolving innovations that cater to modern, complex needs. Diving into the underpinnings of grinding ball mills, it's crucial to acknowledge both the traditional supremacy and the contemporary advancements that render them indispensable.
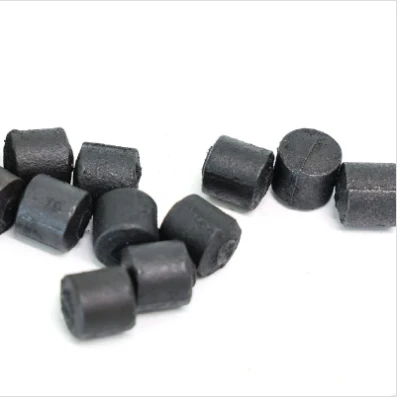
At its core, a ball mill is essentially a cylindrical device used in grinding or mixing materials like ores, chemicals, and ceramic raw materials. Its fundamental mechanism involves the rotation of a cylinder with steel grinding balls, which fall back into the cylinder and onto the material to be ground. One may consider this a brute force method; however, it results in the finely tuned particles essential for precise material properties.
Experience and continual research have demonstrated that the operational efficiency of grinding ball mills can greatly influence overall production costs and product quality. Common challenges like energy consumption, wear and tear, and particle distribution have been primary foci of improvement efforts. Industry experts have discovered through empirical studies that optimizing factors like the rotation speed, ball size distribution, and water content can significantly enhance operational outcomes.
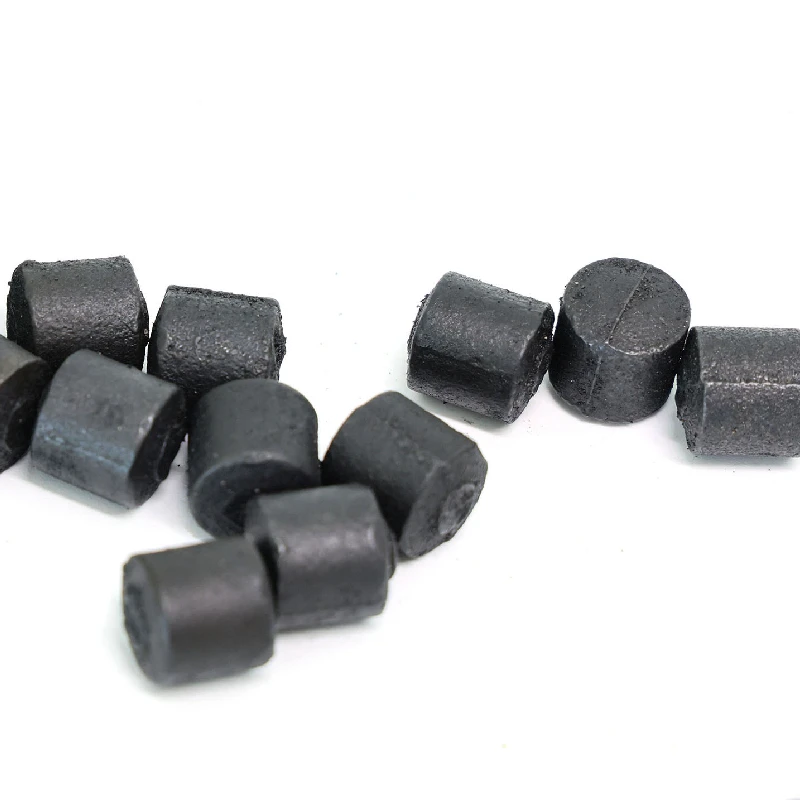
Expertise in manipulating these variables often distinguishes proficient operations from mediocre ones. Professionals in the field understand that a meticulous calibration of each element in the milling process can lead to substantial gains in performance. For instance, altering the rotational speed can affect the material's texture, while fine-tuning the ball size can manage the blend of finer particles and coarser compounds. Ultimately, this expertise helps industries adapt more nimbly to varying demand specifications.
grinding ball mill
Authoritative studies published in peer-reviewed journals underpin the ongoing development of grinding ball mill technologies. Researchers utilize advanced computational models to predict outcomes based on varied input parameters, continually refining the process. These authoritative sources not only guide contemporary industry practices but also set benchmarks for enhanced material processing techniques.
Trustworthiness remains a cornerstone in selecting the appropriate grinding ball mill for specific industrial requirements. Reputable manufacturers invest heavily in R&D, boasting certifications and adhering to stringent quality control protocols. Their equipment undergoes exhaustive testing to ensure reliability and durability, promising clients a consistent output and long-term dependability.
Moreover, innovations like automation and real-time monitoring have modernized traditional ball mills, offering users greater control and efficiency. Integration with AI and advanced sensing technologies allows for predictive maintenance and operational optimization, reducing downtime and maintaining peak productivity.
In conclusion, while the core mechanics of grinding ball mills have remained largely unchanged, their adaptation and evolution through technological advancements continue to uphold their critical role in material processing industries. When assessing a grinding ball mill's suitability, verification through empirical evidence, backed by authoritative expertise and a commitment to quality, ensures that operations achieve the necessary precision and efficiency for optimal productivity.