Selecting the optimal grinding ball size is crucial for maximizing the efficiency and economy of any grinding process, and its importance cannot be overstated. Grinding media directly impacts product quality, grinding efficiency, and energy consumption, making a well-informed selection process instrumental in maintaining competitive advantage.
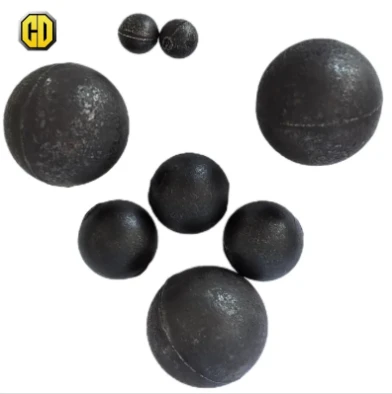
The significance of choosing the correct grinding ball size starts with understanding the dynamics of the material being processed. Each material has distinct physical and mechanical properties that directly influence grinding performance. An expert assessment is essential to analyze the material’s hardness, density, and granularity, as these factors determine the optimal size for grinding media. Smaller balls are effective for achieving finer particle distributions, while larger balls are beneficial for coarser grinding needs.
Real-world experience highlights the importance of equipment compatibility. Grinding machines, whether ball mills or rod mills, have unique requirements regarding media size. Industry professionals underscore the need for media that complements the mill's design, enhancing the grinding process and promoting energy efficiency. For instance, in a scenario where a finer grind is desired, and the ball mill operates efficiently with small grinding balls, operators have witnessed substantial energy savings and improved throughput.
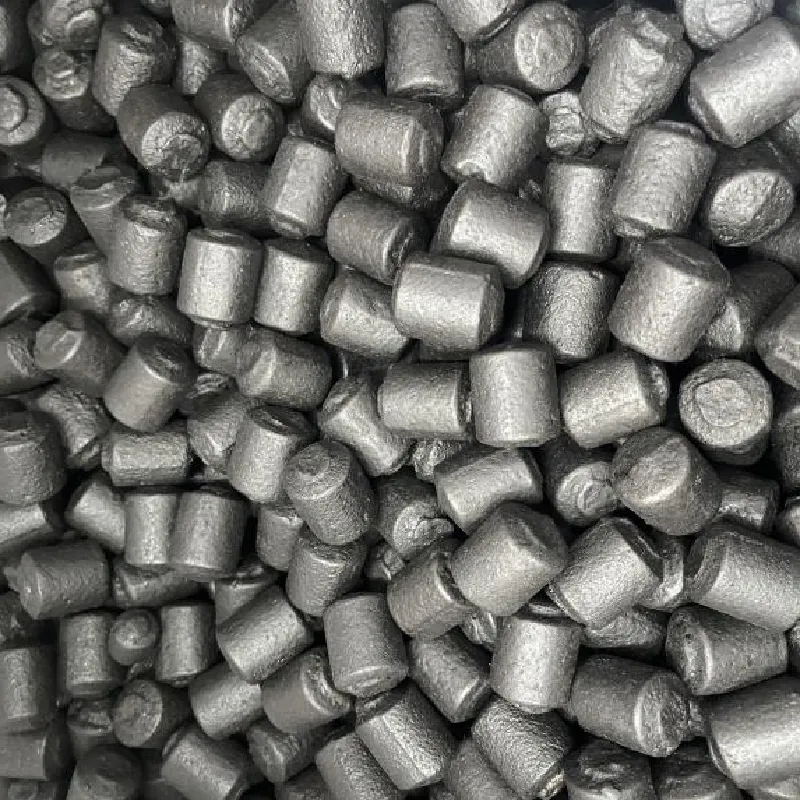
From a technical perspective, expertise in the field recommends a trial-and-error approach combined with theoretical calculations to pinpoint the best grinding ball size. It is advisable to utilize Bond’s formula, a widely respected equation in the industry, which takes into account relevant material characteristics and grinding machine attributes to determine appropriate media size. Professionals often complement this formula with pilot trials to observe performance under real operational conditions, balancing theoretical insights with practical validations.
grinding ball size selection
Authority within the industry reveals that a methodical approach towards grinding ball size selection yields longer equipment lifespan and reduced operational costs. Skilled specialists frequently share success stories of optimized grinding circuits, where strategic selection of media size directly contributed to reduced wear and tear, lower energy requirements, and improved final product quality. These authoritative insights serve as a benchmark for best practices, ensuring smoother operations and higher returns on investment.
Trustworthiness is built when manufacturers and operators adopt transparent selection processes reinforced by empirical evidence. Reliable vendors provide technical data sheets and offer consultation services to guide milling operators through the complex decision-making process. Emphasis is placed on verifiable performance data and customer testimonials that demonstrate clear benefits such as enhanced milling efficiency and superior product quality.
In conclusion, the process of selecting the right grinding ball size is a multifaceted decision that requires a blend of expertise, empirical research, and operational insights. The rewards of implementing a well-calculated selection process are numerous, ranging from improved grinding efficiency and product quality to broader energy savings and operational cost reductions. Industry professionals are encouraged to leverage authoritative resources and data-driven strategies to ensure their selection processes not only meet but exceed the rigorous demands of modern milling operations. Through a commitment to accuracy and industry best practices, companies can secure a distinct competitive edge in their respective markets.