Grinding balls, essential components in the milling industry, play a pivotal role in breaking down materials to the desired particle sizes, ensuring optimal performance in various industrial processes. These spherical, often metallic, entities are meticulously crafted to meet the rigorous demands of numerous sectors, ranging from mining to cement manufacturing. With technology evolving, the manufacture and application of grinding balls have seen tremendous advancement, making it imperative to understand their dynamics for optimized utilization.
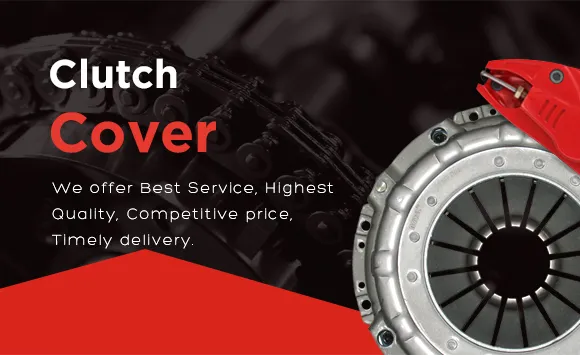
The production of grinding balls, particularly for milling, demands a deep understanding of metallurgical principles. These balls are typically manufactured from high-quality steel or alloys that offer superior wear resistance and toughness. The choice of material significantly impacts their durability and functionality. High-carbon steels, alloy steels, and stainless steels are commonly used due to their exemplary hardness and resistance to wear. Additionally, the manufacturing process involves carefully controlled heat treatments to enhance the balls' mechanical properties, ensuring they withstand the intense pressures and temperatures typical of mill operations.
One aspect of grinding balls that underscores their industrial relevance is their uniformity in shape and size. A constant diameter is crucial for maintaining consistency in particle size reduction, which is essential for downstream processes. Inconsistent sizes can lead to inefficient milling and higher energy consumption, impacting productivity and cost efficiency. Hence, manufacturers invest in precision engineering techniques to ensure grinding balls meet strict geometric tolerances.
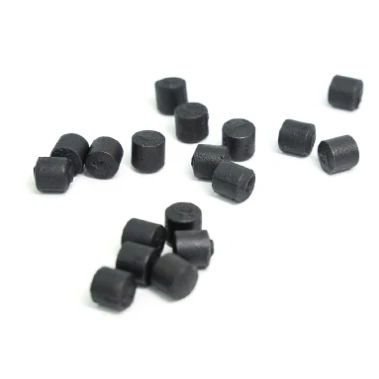
From a practical experience standpoint, industries that rely heavily on milling, like mining, iron ore processing, and cement production, acknowledge that optimal grinding media selection is critical. Mining operators, for instance, report that the right choice of grinding ball can significantly enhance ore extraction efficiency and reduce energy consumption, thereby lowering operational costs. The economic implications are vast, considering the large volumes processed in these industries.
bola de molienda
Expertise in the application of grinding balls goes beyond their material composition and size.
It involves understanding the specific requirements of each milling process. For instance, in semi-autogenous grinding (SAG) mills, the dynamic nature of the milling environment requires grinding balls that can survive impactful collisions without compromising structural integrity. Industry specialists advocate for regular assessments and testing of grinding media to ensure ongoing efficiency and to preempt failures that could disrupt production.
From an authoritative standpoint, the significance of grinding balls is documented in numerous industry guidelines and research studies, which discuss their impact on milling operations and material processing efficiency. Leaders in the field, such as Brunel University London and the University of Queensland's Sustainable Minerals Institute, frequently publish findings that highlight advancements in grinding ball technology and application methodologies, reinforcing their centrality in industrial processes.
Trust in grinding balls is established through stringent quality assurance practices. Reputable manufacturers subject their products to rigorous testing, including impact resistance tests, abrasion resistance evaluations, and hardness measurements to guarantee performance standards are consistently met. These quality credentials are vital in industries where the reliability of structural components can make or break operational success.
Ultimately, the future of grinding balls lies in continued innovation, with research focused on developing more cost-effective materials and environmentally sustainable manufacturing processes. The quest for efficiency and effectiveness pushes the boundary of traditional practices, promising advancements that will benefit industries reliant on precision milling. By keeping pace with these technological strides and adopting best practice frameworks, businesses can harness the full potential of grinding balls, turning them into tantamount assets for industrial excellence.