Forged grinding balls are an essential component in the mining and milling industries, playing a vital role in the grinding process of raw materials. These robust spheres are designed to withstand the intense mechanical forces that break down ores into finer particles. The effectiveness of a grinding ball in contributing to an efficient milling operation is contingent upon its ability to maintain a balance between hardness and durability.
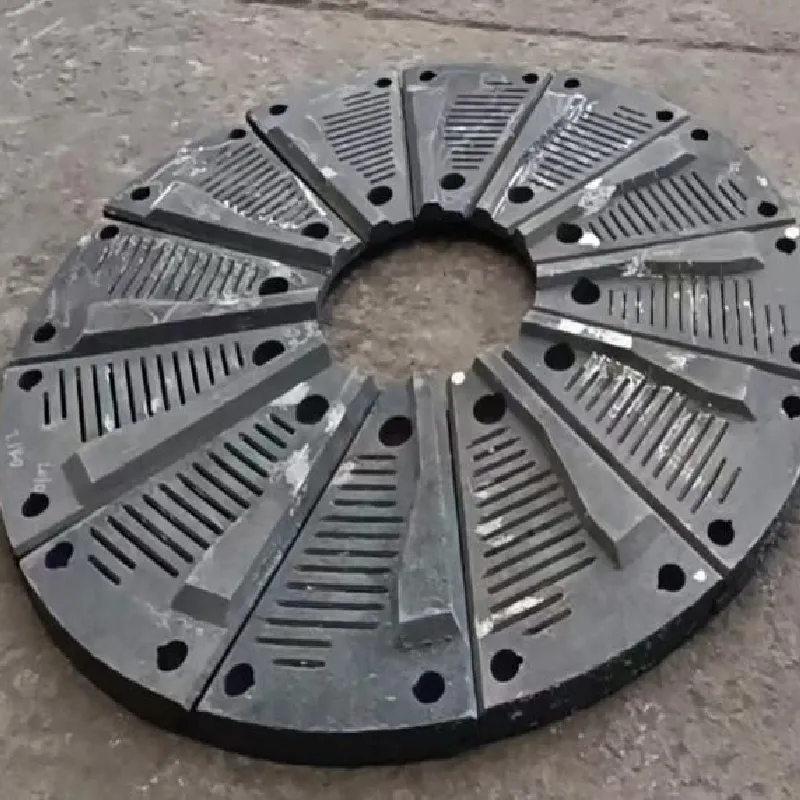
One key aspect of forged grinding balls is their manufacturing process, which involves heating steel billets to a high temperature and then shaping them into ball forms through a forging process. This method offers distinct advantages over other methods such as casting. The forging process ensures a more uniform microstructure and better mechanical properties, which translates into enhanced performance and longer wear life.
In the realm of mining operations, the quality of forged grinding balls is non-negotiable. The selection of materials for these balls is meticulous, often involving high carbon and chromium alloys. These materials are chosen for their ability to achieve the desired hardness and wear resistance. A testament to their durability is their frequent usage in processing the hardest ores found around the globe, from copper and gold to iron and platinum.
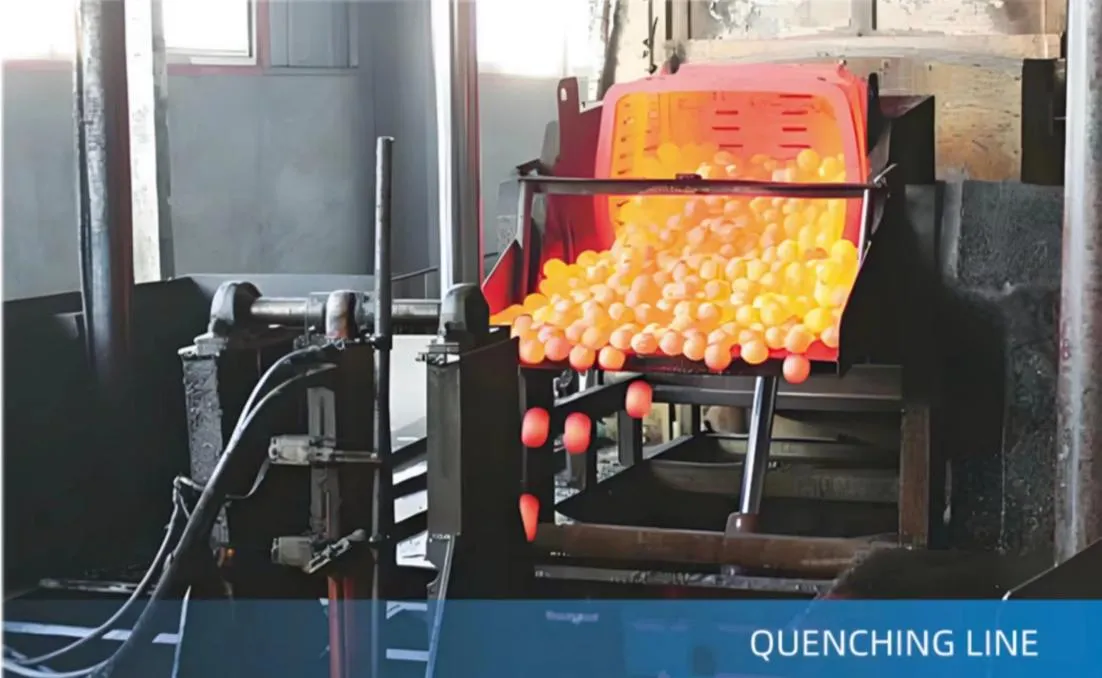
A critical factor in choosing the right grinding ball is its hardness. Measured using the Rockwell or Vickers scale, the hardness of a ball influences its wear rate and impact performance. Balls that are too hard can lead to excessive wear on the mill liners, while those that are too soft can deform under the stress of grinding. Therefore, achieving the optimal hardness is a fine balance that manufacturers must master. Companies often resort to heat treatment processes to achieve the desired hardness, using techniques such as quenching and tempering.
Beyond hardness, the size and weight of the forged grinding balls are tailored to the specific needs of the milling process they are intended for. Balls too large might not interact efficiently with smaller milling equipment, while smaller balls may not be suitable for larger grinding tasks involving coarser ores. An optimal size ensures not only efficient grinding but also energy savings, which are crucial in large-scale operations where energy costs are significant.
bolas de molienda forjadas
The expertise of the manufacturer also plays a pivotal role. Leading producers in the industry employ rigorous testing protocols to ensure their products meet the high standards expected in mining environments. This involves not just initial manufacturing but continuous quality checks throughout the production cycle. Manufacturers utilize sophisticated equipment to simulate real-world grinding conditions, allowing them to refine their products and improve wear rates continually.
Trust in the product is bolstered by certifications and adherence to industry standards. Forged grinding ball manufacturers often align with international standards like ISO 9001 to demonstrate their commitment to quality assurance. Clients can view these certifications as a testament to the manufacturer's reliability and attention to producing high-quality products.
Furthermore, the environmental impact of grinding balls is gaining attention, with manufacturers striving to reduce their carbon footprint. By investing in advanced production techniques and recycling methods, companies are making strides towards more sustainable manufacturing processes. This not only benefits the environment but also aligns with the sustainability goals of many mining companies, enhancing the trustworthiness of the manufacturer.
In conclusion, forged grinding balls are a fundamental tool in the mining sector, necessitating a blend of experience, expertise, authoritativeness, and trustworthiness from manufacturers. The production process, choice of materials, attention to mechanical properties, and adherence to industry standards all contribute to delivering a product that meets the rigorous demands of modern mining operations. Customers seeking quality grinding solutions should consider these factors to ensure they are investing in products that offer efficiency, durability, and a commitment to sustainability.