Mining has evolved significantly over the centuries, adapting to new technologies and techniques. Among the many advancements, Mahlkugeln, known as grinding balls, play a crucial role in enhancing mining operations. These small yet mighty components are vital in crushing ores to extract precious minerals, making them indispensable in the mining sector.
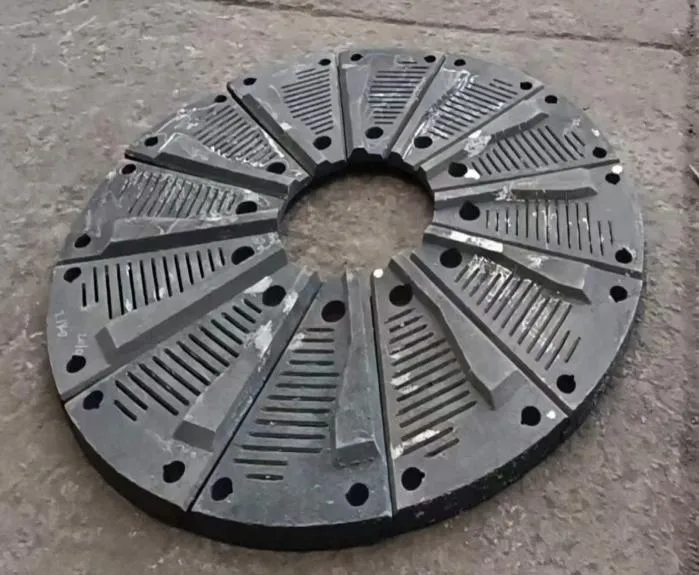
Grinding balls, typically made from durable materials like steel or ceramic, are designed to withstand the rigors of mining environments. Their spherical shape and robust composition allow them to grind ores efficiently, leading to optimal extraction of resources. The choice of material for Mahlkugeln is critical, as it directly impacts the grinding efficiency and longevity. Steel grinding balls, for instance, are favored for their high impact resistance and durability, while ceramic balls are chosen for their resistance to wear and tear and chemical resilience.
In mining operations,
the use of Mahlkugeln has demonstrated significant improvements in productivity. By ensuring the consistent reduction of ore to fine particles, these grinding balls facilitate better separation of valuable minerals from waste material. This precision in the milling process reduces energy consumption and minimizes equipment wear, translating into cost savings and enhanced profitability for mining companies.
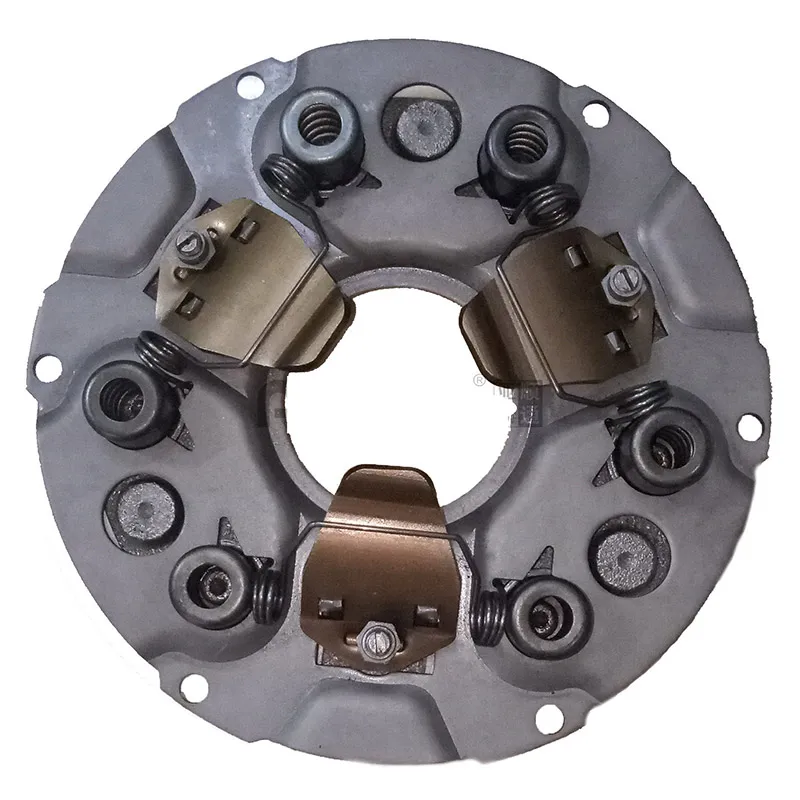
Field experts highlight the importance of selecting the right size and material of Mahlkugeln to match the specific requirements of the milling process. Customization is key, as different mining applications demand varying degrees of hardness and density in grinding balls. Experts often recommend a thorough analysis of the milling environment and the ore characteristics to determine the optimal Mahlkugeln specifications. This tailored approach ensures maximum efficiency and longevity, thereby ensuring a sustainable and productive mining operation.
mahlkugeln bergbau
Trustworthiness in grinding ball production is paramount, given the critical role these components play in mining. Reputable manufacturers adhere to stringent quality standards, employing advanced forging and heat treatment technologies to produce Mahlkugeln that meet industry demands. Certification and rigorous testing protocols further assure mining companies of the reliability and performance of their grinding balls.
Professionals in the field assert the need for continuous innovation in Mahlkugeln design and production. As mining depths increase and ores become harder to reach, the demand for more sophisticated and efficient grinding solutions grows. Research and development efforts focus on enhancing the composition and structure of grinding balls to improve their impact resistance, wear rate, and energy efficiency. Innovations such as the use of hybrid materials and nanotechnology are poised to revolutionize the future of grinding balls, offering unprecedented performance enhancements.
Sustainability is another crucial aspect driving the evolution of Mahlkugeln in mining. The industry recognizes the need to minimize environmental impact and is increasingly turning towards eco-friendly manufacturing processes. This includes the recycling of used grinding balls and reducing the carbon footprint associated with their production and transportation. Sustainable practices not only contribute to environmental stewardship but also enhance the reputation and social responsibility credentials of mining companies.
In conclusion, Mahlkugeln are more than just tools in the mining industry; they are pivotal elements that dictate the efficiency and success of mineral extraction processes. Through expert selection, cutting-edge production techniques, and a commitment to sustainability, mining operations can harness the full potential of grinding balls. As the industry continues to face challenges and opportunities, Mahlkugeln will remain at the forefront, driving advancements and ensuring that mining operations meet the demands of the modern world with precision and efficiency.