The world of industrial milling has always been complex, but the choice of grinding balls, specifically for ball mills, often stands out as a focal point for enhancing efficiency. Mahlkugeln, or grinding spheres, hold substantial authority in this realm due to their crucial role in determining the quality of milling processes.
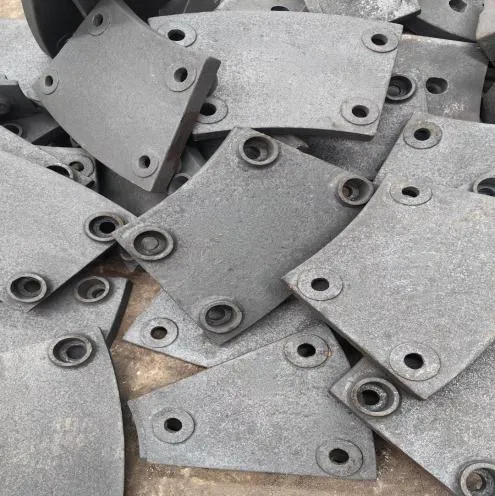
Precision in choosing Mahlkugeln is foundational to achieving optimal milling results. The expertise required in understanding the properties of these spheres—such as hardness, size, and material composition—cannot be underestimated. Grinding balls are often made from various alloys and ceramics, each offering distinct benefits depending on the application. High-chromium steel grinding balls, for example, offer exceptional durability and are suited for scenarios where wear resistance is critical. Their uniform hardness and resistance to corrosion make them a reliable choice in mining and cement industries where materials can be particularly abrasive.
An authoritative selection of Mahlkugeln begins with assessing the specific needs of the ball mill. The size of the grinding spheres must correspond to the mill's size and the desired particle size of the output. Experts often advise aligning the ball size with the ore size to enhance milling efficiency. A general rule of thumb is utilizing balls that are larger than the largest pieces of ore, which helps in breaking down the ore more effectively.
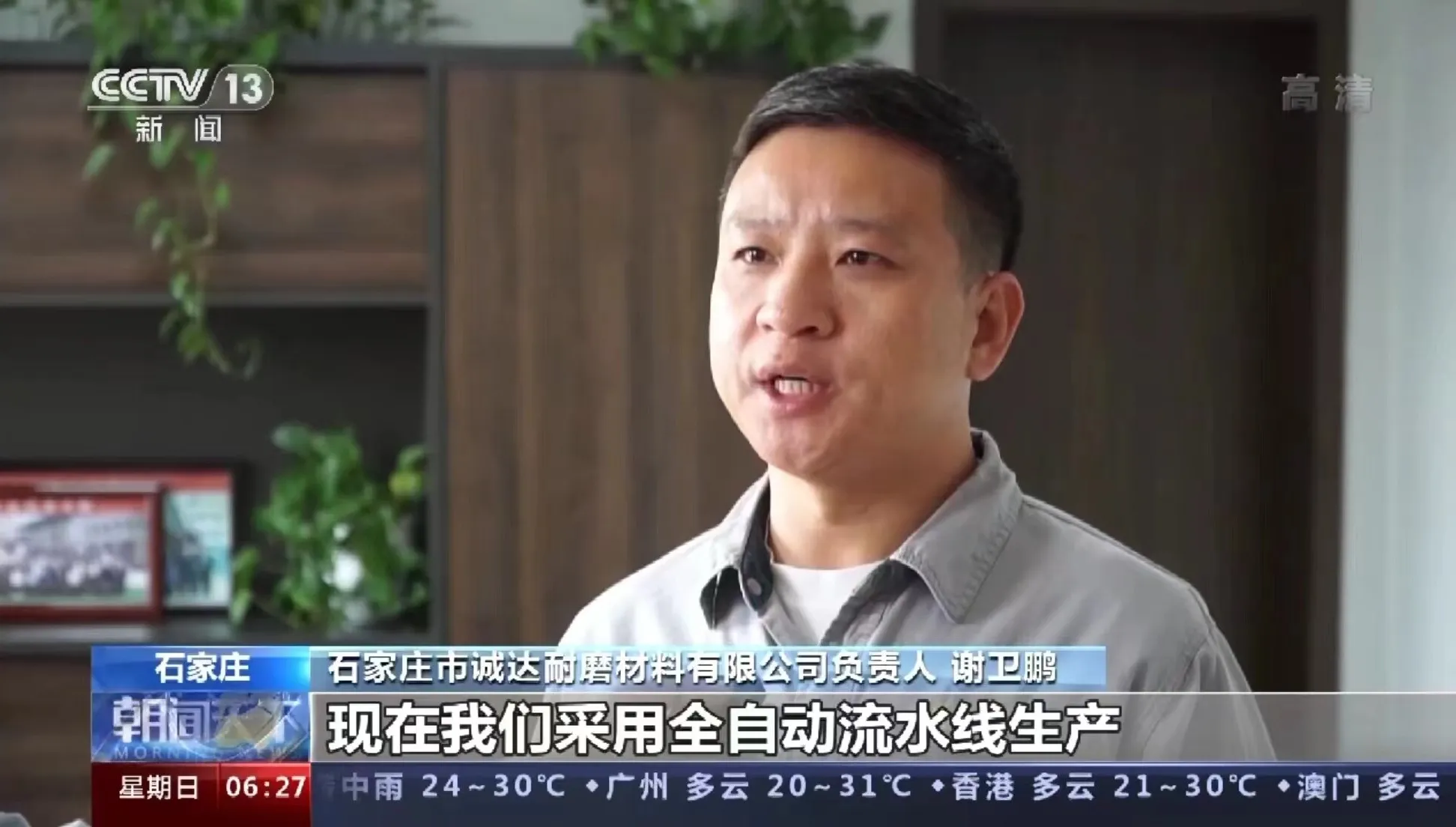
Trustworthiness in choosing the right Mahlkugeln also hinges upon the supplier's reputation. Renowned manufacturers provide detailed specifications, certifications, and assurances about the purity and performance of their grinding spheres. This trust is built over years of consistent product quality and adherence to international standards. Choosing a dependable brand not only ensures the longevity of the equipment but also guarantees a consistent product yield, minimizing downtime and maintenance costs.
grinding balls for ball mill
Real-world experience underlines the importance of ongoing testing and adjustment when using Mahlkugeln for ball mills. Operators often maintain a dynamic approach, carefully observing milling results and making necessary changes to the grinding media size or material as needed. This proactive management ensures adaptability to varying ore types and milling conditions, which can fluctuate over time due to changes in raw material sources or operational parameters.
The experience shared by industry veterans often highlights the importance of regular monitoring and renewal of grinding spheres. Over time, wear and tear inevitably affect the performance of Mahlkugeln, and replacing them at the right intervals can dramatically enhance milling efficiency. Some operations implement continuous monitoring systems to track the wear patterns on grinding media, using this data to optimize the timing of replacements.
Furthermore, innovations in technology have facilitated more precise control over milling operations. Advanced simulation software now allows engineers to model different scenarios and predict the wear patterns of Mahlkugeln with high accuracy. Such tools enable operators to preemptively address potential inefficiencies and adjust the milling process to optimize output, ensuring the highest levels of efficiency are maintained without unpredictable downtimes.
In conclusion, the role of Mahlkugeln in ball mills is pivotal, demanding both expertise and experience to maximize milling performance. Through careful selection, ongoing monitoring, and leveraging technological advancements, industries can secure an authoritative edge in their milling operations. As a cornerstone of efficient industrial processes, the right choice of grinding spheres not only contributes to operational success but also reinforces trust in the overall production process.