Ball mill grinding has become an integral process in various industrial domains, ranging from mining to ceramics, and one essential component of this operation is the ball mill ball. Understanding the nuances of selecting, using, and maintaining these spheres is critical for optimizing outputs while minimizing costs.
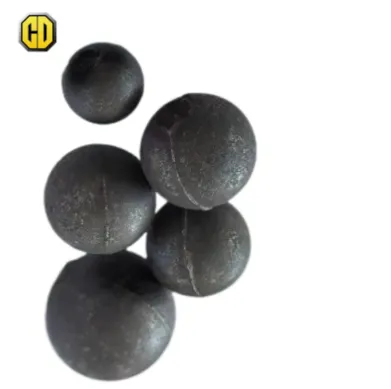
Ball mill balls, primarily composed of steel, ceramic, or other high-performance alloys, are a fundamental part of the grinding media.
Each material has its unique advantages. Steel balls are favored given their heavy nature and hardness, providing a robust grinding action. Conversely, ceramic balls, while lighter, offer impressive wear resistance and are typically used when contamination is a concern due to their chemically inert nature.
It is paramount for industries to select the appropriate ball type and size. This choice is dictated by various factors including the material to be ground, the grinding process (wet or dry), and the desired particle size of the finished product. Larger balls are adept for crushing and breaking larger materials, while smaller balls are more effective for achieving finer grinds.
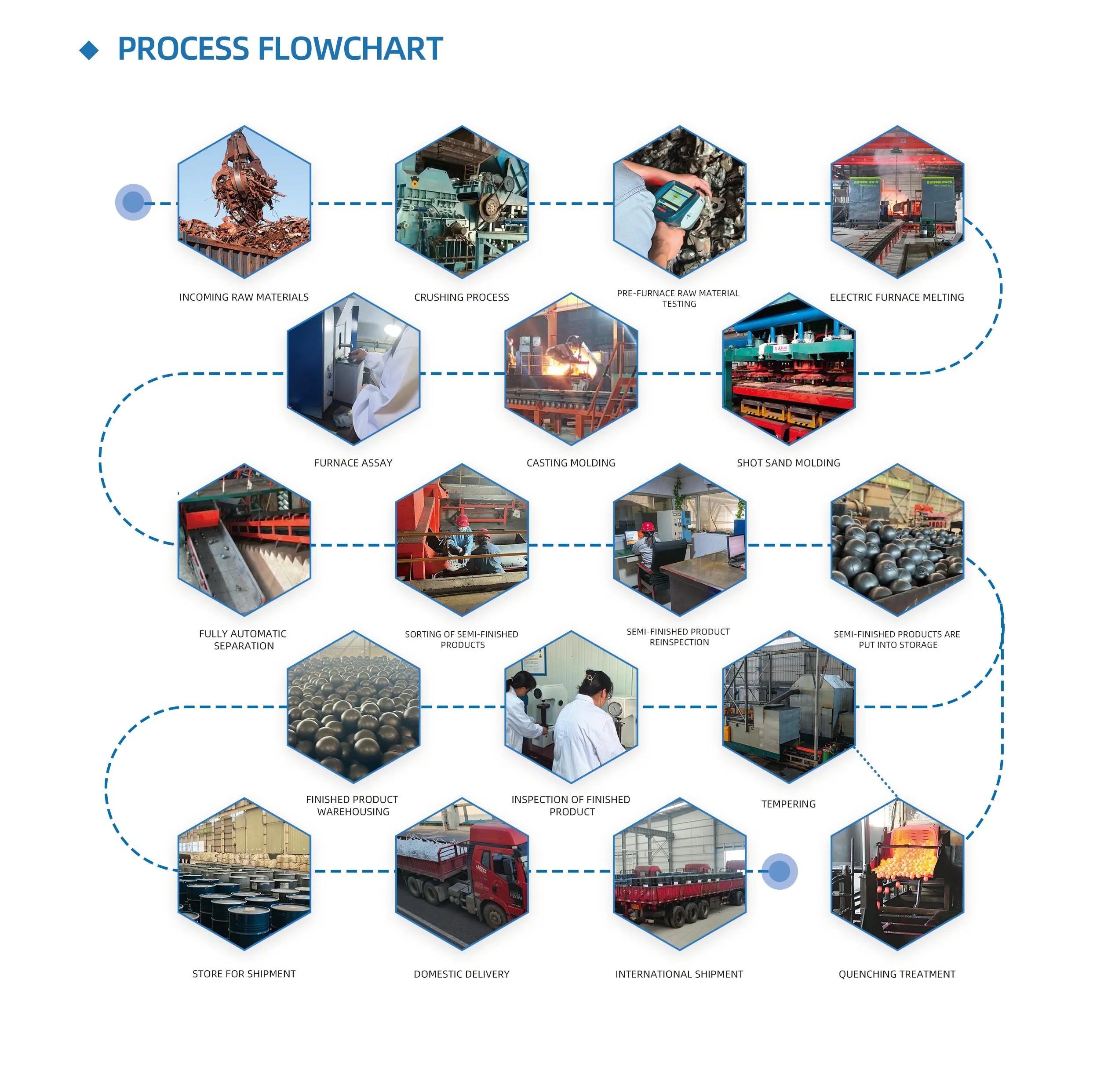
A critical aspect of expertise in working with ball mill balls lies in balancing wear rates. Over time, any grinding media will wear down. Operators must measure and adjust the volume of balls to ensure consistent milling results. Applying a systematic approach can greatly extend the life of both the media and the mill linings. Operators often replenish the ball load based on empirical data collected from regular inspections.
Additionally, correct operation procedures are quintessential. This includes maintaining an optimal rotation speed of the mill. If the speed is too high, it could lead to excessive wear and tear as well as inefficient grinding, while a speed too slow might compromise the quality of the grinding. Consistent monitoring and adjustments by experienced personnel help in achieving maximum operational efficiency and life span.
bolas de moinho de bolas
Furthermore, purchasing high-quality balls from reputable manufacturers ensures not only longevity but trustworthiness in performance. Reputable brands often provide balls that have undergone thorough testing for durability, roundness, and uniformity in composition, which bolster the milling process's reliability.
Innovation in material technology continues to emerge, offering new possibilities in the design and application of ball mill balls. Researchers are developing alloys that not only resist wear but also enhance grinding efficiency. As such trends advance, keeping abreast with new developments and incorporating them into existing systems exemplifies authoritative operation.
Trustworthiness within this domain is further emphasized through sustainable practices. Adopting environmentally friendly ball materials can reduce the carbon footprint of milling operations, aligning industrial practices with today's ecological priorities.
In essence, optimizing the use of ball mill balls is a multi-faceted endeavor that integrates deep industry know-how, ongoing assessment, and a commitment to using high-caliber materials. By focusing on these areas, industries can refine their processes, reducing costs, and enhancing their output quality, establishing themselves as leaders in their respective fields.